Manufacturing method for composite bamboo tube with interchangeable firm joints
A manufacturing method and bamboo tube technology are applied to manufacturing tools, wood processing utensils, reed/straw treatment and other directions, which can solve the problems of large variation of bamboo height taper, irregular diameter and size, etc., and achieve simple production process, light weight, high growth short term effect
- Summary
- Abstract
- Description
- Claims
- Application Information
AI Technical Summary
Problems solved by technology
Method used
Image
Examples
Embodiment 1
[0026] A kind of manufacture method that the end of bamboo tube is convenient to connect is as follows:
[0027] (1) End treatment of round bamboo: select the bamboo tube with a diameter of 76-90mm without bending, cut it into 750mm, dig out 3mm of the bamboo yellow part near the upper 140mm, and chamfer the outer circle of the end by 3mm, and then It is sawed into 4 arc-shaped bamboo slices, the length of separation is 140mm near the end, and the bottom of the groove is a circular hole larger than the notch.
[0028] (2) Variable cross-section at the end of round bamboo: heat-treat the bamboo in a saturated steam pressure tank at a temperature of 180°C for 15 minutes, and bend the arc-shaped bamboo pieces at the end of the bamboo inwards to form the shape, and compress the end to an outer diameter The ring shape of 70mm fits exactly with the diameter of the corresponding assembly hole. And dry it to a moisture content of 10-15%.
[0029] (3) Solid standardization treatment ...
Embodiment 2
[0031] A kind of manufacture method that the end of bamboo tube is convenient to connect is as follows:
[0032] (1) End treatment of round bamboo: choose fresh moso bamboo tubes with a diameter of 80-100mm without bending, saw and cut them into 2400mm, dig out 3mm of the bamboo yellow part near the upper 200mm, and chamfer the outer circle of the end by 3mm, and then It is sawed into 8 arc-shaped bamboo slices, the separation length is 200mm near the end, and the bottom of the groove is a circular hole larger than the notch.
[0033] (2) Variable cross-section at the end of round bamboo: heat-treat the bamboo in a saturated steam pressure tank at a temperature of 180°C for 12 minutes, and bend the arc-shaped bamboo pieces at the end inwards to shape the end, and compress the end to an outer diameter The ring shape of 70mm fits exactly with the diameter of the corresponding assembly hole. And dry it to a moisture content of 10-15%.
[0034] (3) Solid standardization treatmen...
PUM
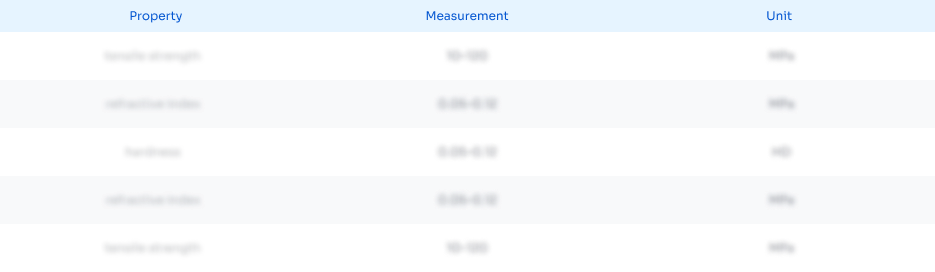
Abstract
Description
Claims
Application Information

- R&D Engineer
- R&D Manager
- IP Professional
- Industry Leading Data Capabilities
- Powerful AI technology
- Patent DNA Extraction
Browse by: Latest US Patents, China's latest patents, Technical Efficacy Thesaurus, Application Domain, Technology Topic, Popular Technical Reports.
© 2024 PatSnap. All rights reserved.Legal|Privacy policy|Modern Slavery Act Transparency Statement|Sitemap|About US| Contact US: help@patsnap.com