Method and system for coproducing isononyl alcohol and C8 alkane
A technology of carbon octane and isononanol, which is applied in the field of co-production of isononanol and carbon octane, can solve the problems that hydroformylation catalysts are difficult to withstand high temperature, threaten process safety, and temperature rise, etc. Possibility of boiling point by-products, effects of high purity and small fluctuations in process temperature
- Summary
- Abstract
- Description
- Claims
- Application Information
AI Technical Summary
Problems solved by technology
Method used
Image
Examples
Embodiment 1
[0040] Example 1 see figure 2 As mentioned above, combined with actual chemical equipment, the present invention provides a specific example of a continuous production of isononanol and carbon octaalkane with a cobalt-phosphine catalyst participating in the catalysis, and carbon octaolefins, carbon monoxide, and hydrogen as raw materials.
[0041] Specifically, this embodiment includes: firstly, the carbonylation and hydrogenation reaction is carried out with carbon monoxide and hydrogen under the catalysis of a cobalt-phosphine catalyst, and the catalyst is cobalt. A phosphine catalyst, the cobalt phosphine catalyst is composed of a cobalt source and a phosphine ligand, and the cobalt phosphine catalyst maintains a Co:P ratio of 3:1, 2:1, 1:1, 1:2, or 3:1~ A certain value in the range of 1:2; too high a Co:P ratio will make the catalyst unstable, but at the same time, too low a Co:P ratio will inhibit the carbonylation / hydrogenation reaction and produce a considerable amount...
Embodiment 2
[0045] Example 2 see figure 2 As shown, firstly, diisobutylene enters the reactor R1 through the pipeline S1 at a flow rate of 1313kg / h from the liquid delivery pump, and carbon monoxide and hydrogen are respectively input into the reactors R1, R2 and R3 at a flow rate of 91kg / h and 15kg / h , the carbonylation / hydrogenation reaction is carried out under the catalysis of cobalt phosphine catalyst, the catalyst is Co 2 (CO) 8 Mixture with phosphine ligand, the phosphine ligand is trioctylphosphine (CAS No. 4731-53-7); keep the Co:P ratio at 1.5, and carry out the pre-preparation process. The pre-preparation process includes the following steps: the Co 2 (CO) 8 Dissolve trioctylphosphine in isononyl alcohol, replace the air with nitrogen, stir the mixture, and fill with CO, H 2 Gas to a pressure of 5MPa, and react at 140°C for 5h to obtain a cobaltphosphine catalyst.
[0046] The reactants flow through the reactors R1, R2, and R3 in sequence, and the reaction temperature is ...
PUM
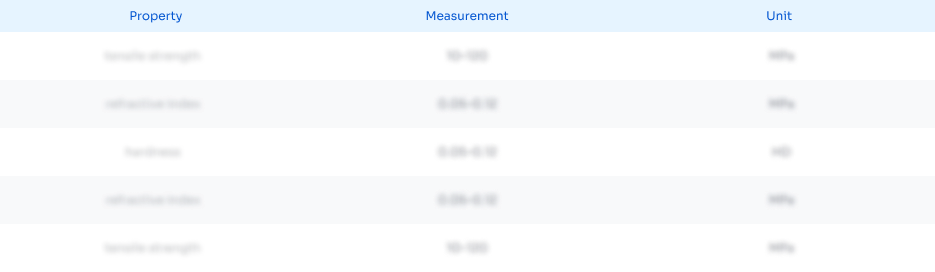
Abstract
Description
Claims
Application Information

- R&D
- Intellectual Property
- Life Sciences
- Materials
- Tech Scout
- Unparalleled Data Quality
- Higher Quality Content
- 60% Fewer Hallucinations
Browse by: Latest US Patents, China's latest patents, Technical Efficacy Thesaurus, Application Domain, Technology Topic, Popular Technical Reports.
© 2025 PatSnap. All rights reserved.Legal|Privacy policy|Modern Slavery Act Transparency Statement|Sitemap|About US| Contact US: help@patsnap.com