Anhydrous treatment process for polycrystalline silicon slurry
A technology of hydration treatment and polycrystalline silicon, which is applied in the direction of inorganic chemistry, silicon compounds, silicon halide compounds, etc., can solve the problems of long process path, inability to directly use, waste of resources, etc., and achieve the effect of improving economy
- Summary
- Abstract
- Description
- Claims
- Application Information
AI Technical Summary
Problems solved by technology
Method used
Image
Examples
Embodiment
[0032] Embodiment A polysilicon slag anhydrous treatment process, comprising the following steps:
[0033] (1) 5000kg of polycrystalline silicon slurry with a moisture content of 70-90% from the upstream enters the vacuum drum filter 1, and the slurry is separated from solid-liquid-gas through the drum surface pre-coated with diatomaceous earth to obtain 4500kg of liquid and gas A and 500kg of solid A respectively .
[0034] 4500kg of liquid and gas A enter the exhaust gas treatment system 11, and 4480kg of liquid A is collected after treatment, and waste gas A is emptied.
[0035] (2) 500kg of solid A enters the dryer 2, heats and stirs with steam at 80-95°C, and obtains 480kg of dried solid product with a moisture content of ≤3% and 20kg of silicon tetrachloride and part of trichlorosilane in gas form.
[0036] 20kg of silicon tetrachloride and part of trichlorosilane in the form of gas are discharged through the top filter of the dryer 2 and enter the tail gas treatment sy...
PUM
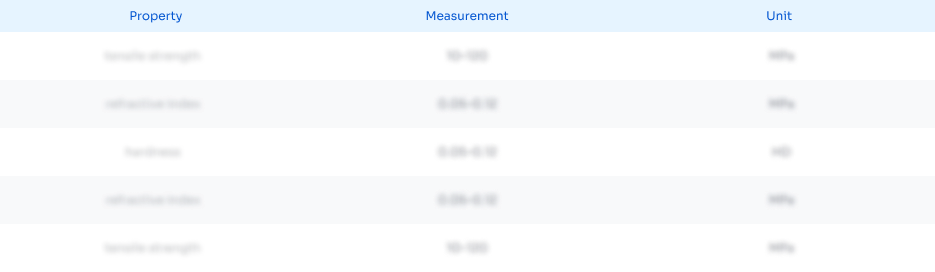
Abstract
Description
Claims
Application Information

- Generate Ideas
- Intellectual Property
- Life Sciences
- Materials
- Tech Scout
- Unparalleled Data Quality
- Higher Quality Content
- 60% Fewer Hallucinations
Browse by: Latest US Patents, China's latest patents, Technical Efficacy Thesaurus, Application Domain, Technology Topic, Popular Technical Reports.
© 2025 PatSnap. All rights reserved.Legal|Privacy policy|Modern Slavery Act Transparency Statement|Sitemap|About US| Contact US: help@patsnap.com