Turn-milling machining process method for gyroscope wire protecting plate
A process method and composite processing technology, applied in the field of mechanical processing, can solve the problems of reducing the processing accuracy and processing quality of parts, long auxiliary processing time for wire guard processing, and no published patent documents are found, so as to reduce the processing difficulty and shorten the processing time. Auxiliary time, effect of shortening auxiliary machining time
- Summary
- Abstract
- Description
- Claims
- Application Information
AI Technical Summary
Problems solved by technology
Method used
Image
Examples
Embodiment Construction
[0043] The embodiments of the present invention will be described in further detail below in conjunction with the accompanying drawings; the present embodiments are descriptive, not restrictive, and cannot thereby limit the protection scope of the present invention.
[0044] First describe the structure of the gyroscope wire guard of the present invention, see figure 2 , 3 , 4, 5, 6.
[0045] The gyroscope wire guard 1 is a disc-shaped structure, and its front structure is as follows: a concentric inner hole 8 is formed in the center of the disc. There are seven identical arc grooves 2, and the inner top of the arc groove is closed with an arc, and the bottom of the arc groove at the closed part of the arc is respectively made with a φ0.8mm I through hole 5 and a II through hole from the inside to the outside. The hole 6 and the through hole 7 of φ1.8mm are formed with three stepped holes 4 of φ3.5-φ1.8mm with the same diameter between the interval arc grooves, and are form...
PUM
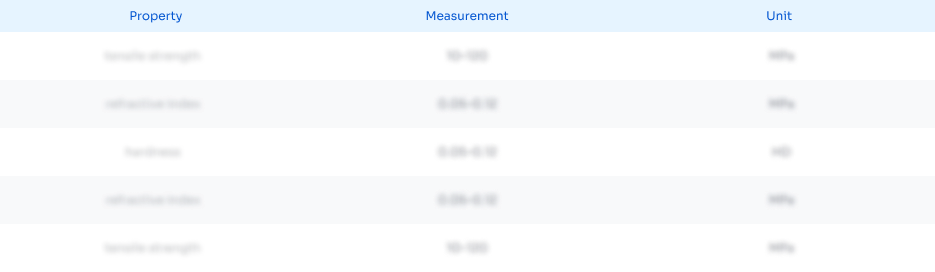
Abstract
Description
Claims
Application Information

- R&D
- Intellectual Property
- Life Sciences
- Materials
- Tech Scout
- Unparalleled Data Quality
- Higher Quality Content
- 60% Fewer Hallucinations
Browse by: Latest US Patents, China's latest patents, Technical Efficacy Thesaurus, Application Domain, Technology Topic, Popular Technical Reports.
© 2025 PatSnap. All rights reserved.Legal|Privacy policy|Modern Slavery Act Transparency Statement|Sitemap|About US| Contact US: help@patsnap.com