Polylactic acid injection molding method
A technology of injection molding and polylactic acid, which is applied in the field of polylactic acid, can solve the problems that hinder the development of polylactic acid, such as wide application of polylactic acid resin, high brittleness, and insufficient toughness, so as to promote catalytic polycondensation and depolymerization, improve reactivity, and strong dehydration Effect
- Summary
- Abstract
- Description
- Claims
- Application Information
AI Technical Summary
Problems solved by technology
Method used
Examples
Embodiment 1
[0033] A polylactic acid injection molding method is characterized in that the method comprises the following steps:
[0034] Step 1, take 0.5g of the first initiator, 10g of polylactic acid intermediate and 60mL of dichloromethane and mix evenly, add 0.08g of N,N-dimethylethanolamine, seal and stir at 30°C for 3 hours, then add 0.1g of benzene Formic acid was stirred and dissolved, precipitated in ethylenediaminetetraacetic acid, recrystallized twice, and vacuum-dried to obtain the primary product of polylactic acid.
[0035] Wherein, the preparation method of polylactic acid intermediate is:
[0036] Weigh 30g of lactic acid and 0.15g of trimethyl orthoformate into a reaction flask, stir and react at room temperature for 3h to obtain product M; wherein, the stirring speed is 300rpm;
[0037] Add 1.4g antimonous chloride to the product M, stir evenly, distill under reduced pressure at 40°C and 0.1Mpa for 2h, depolymerize, dry, and recrystallize to obtain a polylactic acid in...
Embodiment 2
[0048] A polylactic acid injection molding method is characterized in that the method comprises the following steps:
[0049] Step 1, take 0.5g of the first initiator, 10g of polylactic acid intermediate and 60mL of dichloromethane and mix evenly, add 0.08g of N,N-dimethylethanolamine, seal and stir at 30°C for 3 hours, then add 0.1g of benzene Formic acid was stirred and dissolved, precipitated in ethylenediaminetetraacetic acid, recrystallized twice, and vacuum-dried to obtain the primary product of polylactic acid.
[0050] Wherein, the preparation method of polylactic acid intermediate is:
[0051] Weigh 30g of lactic acid and 0.15g of trimethyl orthoformate into a reaction flask, stir and react at room temperature for 3h to obtain product M; wherein, the stirring speed is 300rpm;
[0052] Add 1.4g of antimonous chloride to the product M, stir evenly, distill under reduced pressure at 50°C and 0.1Mpa for 2h, depolymerize, dry, and recrystallize to obtain a polylactic acid...
Embodiment 3
[0063] A polylactic acid injection molding method is characterized in that the method comprises the following steps:
[0064] Step 1, take 0.5g of the first initiator, 10g of polylactic acid intermediate and 60mL of dichloromethane and mix evenly, add 0.08g of N,N-dimethylethanolamine, seal and stir at 30°C for 3 hours, then add 0.1g of benzene Formic acid was stirred and dissolved, precipitated in ethylenediaminetetraacetic acid, recrystallized twice, and vacuum-dried to obtain the primary product of polylactic acid.
[0065] Wherein, the preparation method of polylactic acid intermediate is:
[0066] Weigh 30g of lactic acid and 0.15g of trimethyl orthoformate into a reaction flask, stir and react at room temperature for 3h to obtain product M; wherein, the stirring speed is 300rpm;
[0067] Add 1.4g of antimony chloride to the product M, stir evenly, distill under reduced pressure at 45°C and 0.1Mpa for 2h, depolymerize, dry, and recrystallize to obtain a polylactic acid i...
PUM
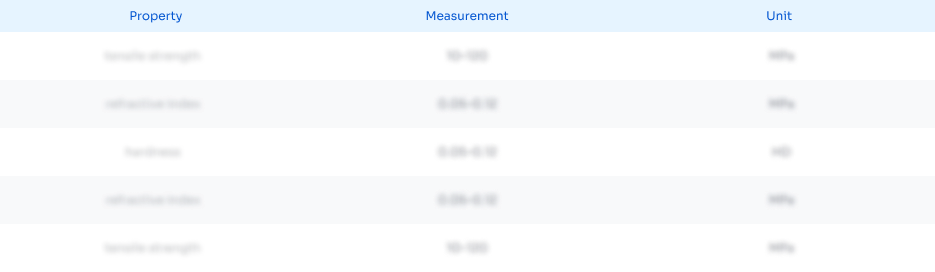
Abstract
Description
Claims
Application Information

- R&D
- Intellectual Property
- Life Sciences
- Materials
- Tech Scout
- Unparalleled Data Quality
- Higher Quality Content
- 60% Fewer Hallucinations
Browse by: Latest US Patents, China's latest patents, Technical Efficacy Thesaurus, Application Domain, Technology Topic, Popular Technical Reports.
© 2025 PatSnap. All rights reserved.Legal|Privacy policy|Modern Slavery Act Transparency Statement|Sitemap|About US| Contact US: help@patsnap.com