Two-component fabricated building sealant and preparation method thereof
A sealant and prefabricated technology, applied in the field of building materials, can solve the problems of secondary cracking, waste, and many processing steps, and achieve the effects of simple preparation method and operation, high material utilization rate, and avoiding secondary cracking.
- Summary
- Abstract
- Description
- Claims
- Application Information
AI Technical Summary
Problems solved by technology
Method used
Image
Examples
preparation example Construction
[0096] 1) Preparation of component A:
[0097] Mix the epoxy resin, reactive diluent and thixotropic agent uniformly under elevated temperature conditions (preferably mix at 50-95°C, more preferably 60-80°C, eg 70°C, preferably stir and mix). After a period of time, start high-speed stirring and vacuumize (for example, the vacuum is -0.01MPa to -0.09MPa), and the high-speed stirring time is 20-60min. Then add the inorganic filler and continue to stir (stir for 15-40min), cool down and stop stirring. After stopping stirring for 30 minutes, stop vacuuming to obtain component A.
[0098] 2) Preparation of polyetheramine modified curing agent:
[0099] Add E-51 epoxy resin dropwise in polyoxypropylene diamine and / or polyoxyethylene diamine and / or polyoxypropylene triamine (preferred drop time 1-3h, preferred reaction 0.1-2h, preferred reaction temperature is not over 75°C, preferably 40-70°C), to obtain polyetheramine modified curing agent I. Preferably, continue to add 0.5-10...
Embodiment 1
[0122] 1) Preparation of component A:
[0123] 52.8g of E-51 epoxy resin, 6.0g of benzyl glycidyl ether and 2.0g of hydrophobic fumed silica were stirred and mixed uniformly under the condition of raising the temperature to 70°C. After 20 minutes, turn on the high-speed stirring and evacuate to -0.09MPa, and the high-speed stirring time is 45 minutes. Then add 40.0g active calcium carbonate and continue to stir for 30min, cool down to room temperature and stop stirring. After stopping stirring for 30 minutes, stop vacuuming to obtain component A.
[0124] 2) Preparation of polyetheramine modified curing agent:
[0125] Stir and mix 12.0g of polyoxypropylene diamine, 15.0g of polyoxyethylene diamine, and 10g of polyoxypropylene triamine to obtain a mixed solution, then add 24.0g of E-51 epoxy resin dropwise to the mixed solution, and the dropping time 2h, the dropwise reaction temperature is 70°C to obtain the polyetheramine modified curing agent I.
[0126] 3) Preparation ...
Embodiment 2
[0130] 1) Preparation of component A:
[0131] 47.0g of E-51 epoxy resin, 4.8g of benzyl glycidyl ether and 1.8g of hydrophobic fumed silica were stirred and mixed uniformly under the condition of raising the temperature to 70°C. After 20 minutes, turn on the high-speed stirring and evacuate to -0.09MPa, and the high-speed stirring time is 45 minutes. Then add 32.0g active calcium carbonate and continue to stir for 30min, cool to room temperature and stop stirring. After stopping stirring for 30 minutes, stop vacuuming to obtain component A.
[0132] 2) Preparation of polyetheramine modified curing agent:
[0133] Stir and mix 12.0g of polyoxypropylene diamine, 15.0g of polyoxyethylene diamine, and 10g of polyoxypropylene triamine to obtain a mixed solution, then add 24.0g of E-51 epoxy resin dropwise to the mixed solution, and the dropping time 2h, the dropwise reaction temperature is 70°C to obtain the polyetheramine modified curing agent I.
[0134] 3) Preparation of co...
PUM
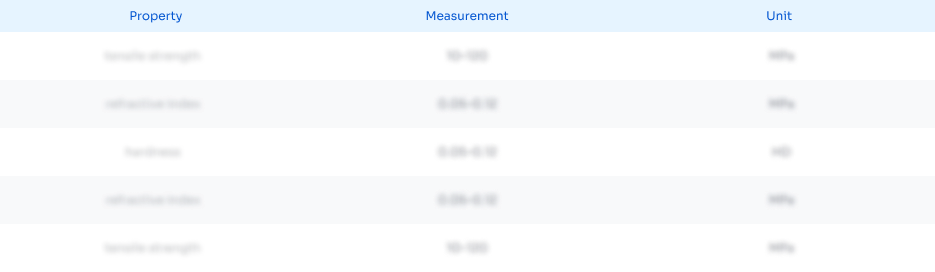
Abstract
Description
Claims
Application Information

- R&D
- Intellectual Property
- Life Sciences
- Materials
- Tech Scout
- Unparalleled Data Quality
- Higher Quality Content
- 60% Fewer Hallucinations
Browse by: Latest US Patents, China's latest patents, Technical Efficacy Thesaurus, Application Domain, Technology Topic, Popular Technical Reports.
© 2025 PatSnap. All rights reserved.Legal|Privacy policy|Modern Slavery Act Transparency Statement|Sitemap|About US| Contact US: help@patsnap.com