Preparation method of high-transmission composite Ag film
A high-transmittance, thin-film technology, applied in the field of preparation of composite Ag thin films, can solve the problems of reduced surface roughness, limited wettability or effectiveness, and achieve good thermal stability
- Summary
- Abstract
- Description
- Claims
- Application Information
AI Technical Summary
Problems solved by technology
Method used
Image
Examples
Embodiment Construction
[0028] The present invention will be further described in detail in conjunction with the accompanying drawings and specific embodiments.
[0029] Step 1: Glass substrate pretreatment: Ultrasonicate the glass substrate in absolute ethanol for 15 minutes, wash with deionized water, soak in cleaning solution for 30-45 minutes, and dry under nitrogen flow
[0030] The cleaning solution is a mixture of ammonia, hydroxide and deionized water in a mass ratio of 1:2:5.
[0031] Step 2: Using the radio frequency magnetron sputtering method with a sputtering power of 120W-140W, the deposition chamber is evacuated to make it less than 1×10 -5 Pa pressure, to preheat the mass flowmeter, DC power supply, and RF power supply, TiO 2 Deposit TiO on the target 2 Thin film, the purity is 99.99%, the working gas is a mixed gas of oxygen and argon, the partial pressure is 1:3, the flow rate is 70sccm, the negative bias voltage is 40V, the deposition time is 2 hours; anneal at 300-500°C after de...
PUM
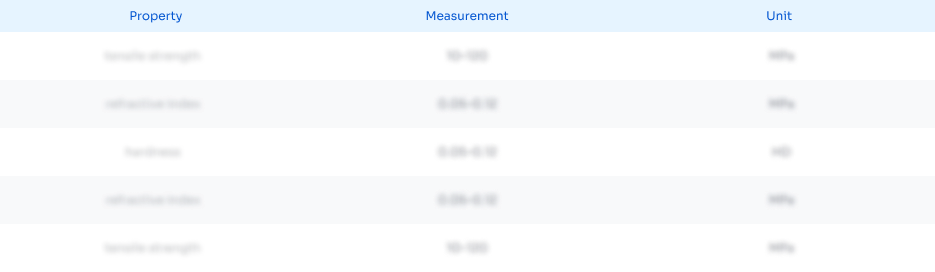
Abstract
Description
Claims
Application Information

- R&D
- Intellectual Property
- Life Sciences
- Materials
- Tech Scout
- Unparalleled Data Quality
- Higher Quality Content
- 60% Fewer Hallucinations
Browse by: Latest US Patents, China's latest patents, Technical Efficacy Thesaurus, Application Domain, Technology Topic, Popular Technical Reports.
© 2025 PatSnap. All rights reserved.Legal|Privacy policy|Modern Slavery Act Transparency Statement|Sitemap|About US| Contact US: help@patsnap.com