Preparation method of interlayer toughened composite material
A technology for toughening composite materials and composite material layers, applied in the field of composite material science, can solve the problems of inability to carry out large-scale promotion and use, increase structural weight and manufacturing costs, increase matrix resin viscosity, etc. Toughness effect, low cost, and the effect of enhancing the interlayer toughness of itself
- Summary
- Abstract
- Description
- Claims
- Application Information
AI Technical Summary
Problems solved by technology
Method used
Image
Examples
Embodiment
[0032] An interlayer toughened composite material board containing agglomerated microcapsules in this embodiment includes fiber prepreg stacks and epoxy resin glue, the epoxy resin glue contains microcapsules, and the resin glue is filled and coated on the surface of the cured prepreg stack. In this embodiment, 10 layers of fiber prepreg with a thickness of 0.15 mm are laid in one direction to form a stack with a thickness of 1.5 mm, and the finally formed interlayer toughened sample is a composite plate structure with a thickness of 3 mm.
[0033] figure 2 It is a schematic diagram of the distribution of microcapsules in the resin matrix. From figure 2 It can be seen that the capsules are distributed in the interlayer resin matrix in the form of agglomeration. During the curing process of placing the sample on a hot press at a high temperature of 120°C and a high pressure of 4Mpa, the capsules are squeezed and ruptured, which induces a polymerization reaction in the capsu...
PUM
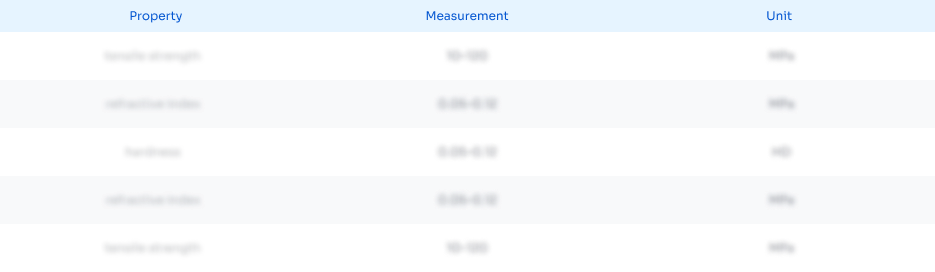
Abstract
Description
Claims
Application Information

- Generate Ideas
- Intellectual Property
- Life Sciences
- Materials
- Tech Scout
- Unparalleled Data Quality
- Higher Quality Content
- 60% Fewer Hallucinations
Browse by: Latest US Patents, China's latest patents, Technical Efficacy Thesaurus, Application Domain, Technology Topic, Popular Technical Reports.
© 2025 PatSnap. All rights reserved.Legal|Privacy policy|Modern Slavery Act Transparency Statement|Sitemap|About US| Contact US: help@patsnap.com