Recovery method of waste SCR denitration catalyst
A technology for denitrification catalysts and waste catalysts, which is applied in the field of recovery of waste SCR denitrification catalysts, and can solve the problems of low recovery rate, difficult industrial application, and efficient recovery of vanadium, etc.
- Summary
- Abstract
- Description
- Claims
- Application Information
AI Technical Summary
Problems solved by technology
Method used
Examples
Embodiment 1
[0031] Embodiment 1 has described a kind of recovery method of waste SCR denitration catalyst, and specific steps include:
[0032] (1) Pretreatment
[0033] Using vanadium-molybdenum-titanium honeycomb waste SCR denitrification catalyst as raw material, first blow off the loose dust attached to the surface by compressed air; use 2wt% fatty alcohol sodium sulfate, 3wt% fatty alcohol polyoxyethylene ether, 1wt% tripolyphosphate Wash the spent catalyst with an aqueous solution of sodium and 1.5 wt% hydrochloric acid, then dry the spent catalyst naturally in the shade; roast the catalyst at 650°C for 5 hours, and finally crush the spent catalyst to a size below 200 mesh for use.
[0034] (2)TiO 2 separate
[0035] Ba(OH) with a mass ratio of 2:1 2 The solid and waste catalyst powder were mixed evenly, and roasted at 700°C for 4 hours; the sintered block was crushed to below 200 mesh, and the powder was leached three times with a dilute hydrochloric acid solution with a volume ...
Embodiment 2
[0046] Embodiment 2 has described a kind of recovery method of waste SCR denitration catalyst, and specific steps include:
[0047] (1) Pretreatment
[0048] Using vanadium-tungsten-titanium honeycomb waste SCR denitrification catalyst as raw material, first blow off the loose dust attached to the surface by compressed air; use 3wt% fatty alcohol sodium sulfate, 5wt% fatty alcohol polyoxyethylene ether, 2wt% tripolyphosphate Wash the spent catalyst with an aqueous solution of sodium and 2wt% hydrochloric acid, then dry the spent catalyst naturally in the shade; roast the catalyst at 550°C for 4 hours, and finally crush the spent catalyst to a size below 200 mesh for future use.
[0049] (2)TiO 2 separate
[0050] Ba(OH) with a mass ratio of 1.5:1 2 Mix the solid and waste catalyst powder evenly, and roast at 800°C for 4 hours; crush the agglomerate to below 200 mesh, and repeat the leaching of the powder 3 times with a dilute hydrochloric acid solution with a volume concent...
Embodiment 3
[0061] Embodiment 3 has described the recovery method of another kind of waste SCR denitration catalyst, and specific steps include:
[0062] (1) Pretreatment
[0063] Using vanadium-molybdenum-titanium flat-plate waste SCR denitrification catalyst as raw material, the loose dust attached to the surface is first blown off by compressed air; Wash the waste catalyst with an aqueous solution of sodium phosphate and 3wt% hydrochloric acid, and then dry the waste catalyst naturally in the shade; roast the catalyst at 700°C for 4 hours, separate the catalyst from the metal mesh by shaking and scraping, collect the detached waste catalyst and crush it to 200 mesh The following spare.
[0064] (2)TiO 2 separate
[0065] Ba(OH) with a mass ratio of 2.5:1 2 Mix the solid and spent catalyst powder evenly, and roast at 750°C for 3 hours; crush the agglomerate to below 200 mesh, and repeat the leaching of the powder 4 times with a dilute hydrochloric acid solution with a volume concent...
PUM
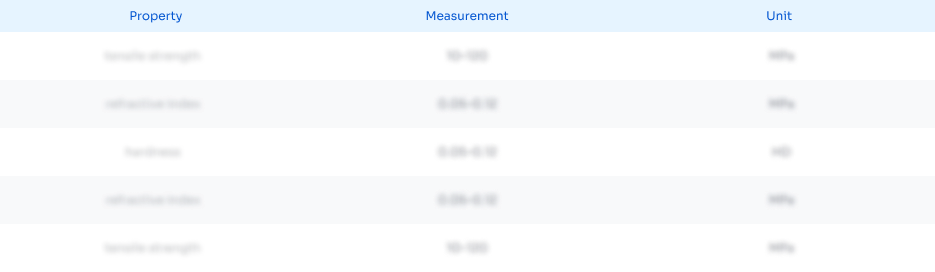
Abstract
Description
Claims
Application Information

- Generate Ideas
- Intellectual Property
- Life Sciences
- Materials
- Tech Scout
- Unparalleled Data Quality
- Higher Quality Content
- 60% Fewer Hallucinations
Browse by: Latest US Patents, China's latest patents, Technical Efficacy Thesaurus, Application Domain, Technology Topic, Popular Technical Reports.
© 2025 PatSnap. All rights reserved.Legal|Privacy policy|Modern Slavery Act Transparency Statement|Sitemap|About US| Contact US: help@patsnap.com