Preparation method of porous carbon material with high thermal-oxidative stability and regular pore structure
A porous carbon material and pore structure technology, which can be used in the preparation/purification of carbon, chemical instruments and methods, carbon compounds, etc., can solve the problems of disordered pore structure, poor thermal and oxygen stability, etc. The effect of improved oxygen stability and adjustable specific surface area
- Summary
- Abstract
- Description
- Claims
- Application Information
AI Technical Summary
Problems solved by technology
Method used
Image
Examples
Embodiment 1
[0027] 1. Using 25mmol of acetic acid as a catalyst, dissolve 10mmol of pyroglucinol and 15mmol of p-phenylenediamine in 10mL of 1,4-dioxane, react in vacuum at 120°C for 3 days, filter with suction and wash with acetone, 150 ℃ vacuum drying to obtain COFs.
[0028] 2. COFs (1.0 g) were annealed at 450° C. for 30 minutes under argon protection to prepare nitrogen-doped porous carbon (Ncarbon). COFs (0.3g) and B 2 o 3 (3g) was annealed at 300°C for 30min (BNcarbon1), 450°C for 30min (BNcarbon 2), 450°C for 50min (BNcarbon 3), 450°C for 90min (BN carbon 4) and 600°C for 30min (BNcarbon 5) Porous carbon doped with boron and nitrogen is obtained.
[0029] figure 1 It is the thermogravimetric curve of the nitrogen-doped and boron-nitrogen-doped porous carbon materials in Example 1 under air conditions. Depend on figure 1 Known, N carbon in 10wt% mass loss (T 10wt% ) under the temperature of 386.7 ° C, at 50wt% mass loss (T 50wt% ) is 493.0°C, the temperature at the peak val...
Embodiment 2
[0033] 1. Using 12.5 mmol of acetic acid as a catalyst, dissolve 15 mmol of terephthalaldehyde and 10 mmol of melamine in 10 mL of dimethyl sulfoxide, react in vacuum at 180°C for 3 days, filter with suction, wash with acetone, and dry in vacuum at 150°C to obtain COFs.
[0034] 2. COFs (1.0 g) were annealed at 600° C. for 30 minutes under argon protection to prepare nitrogen-doped porous carbon. The mixture of COFs (0.3 g) and phosphoric acid (3 g) was annealed at 300 °C for 30 min, 450 °C for 30 min, 600 °C for 30 min and 750 °C for 30 min to obtain phosphorus and nitrogen doped porous carbon.
Embodiment 3
[0036] 1. With 25mmol of acetic acid as a catalyst, 20mmol of 1,3,5-benzenetriboronic acid and 10mmol of 2,3,6,7,10,11-hexahydroxybiphenyl were dissolved in 8mL of 1,4-dioxane, 120 ℃ vacuum reaction for 3 days, suction filtration and washing with acetone, vacuum drying at 100 ℃ to obtain COFs.
[0037] 2. COFs (1.0 g) were annealed at 600° C. for 30 minutes under argon protection to prepare boron-doped porous carbon. The mixture of COFs (0.3 g) and melamine (1.5 g) was annealed at 300 °C for 30 min, 450 °C for 30 min, 600 °C for 30 min and 750 °C for 30 min to obtain boron and nitrogen doped porous carbon.
PUM
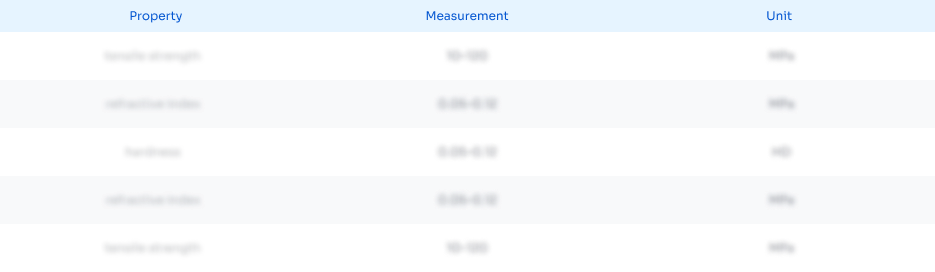
Abstract
Description
Claims
Application Information

- R&D
- Intellectual Property
- Life Sciences
- Materials
- Tech Scout
- Unparalleled Data Quality
- Higher Quality Content
- 60% Fewer Hallucinations
Browse by: Latest US Patents, China's latest patents, Technical Efficacy Thesaurus, Application Domain, Technology Topic, Popular Technical Reports.
© 2025 PatSnap. All rights reserved.Legal|Privacy policy|Modern Slavery Act Transparency Statement|Sitemap|About US| Contact US: help@patsnap.com