A composite briquette binder
A technology of composite briquette and binder, which is used in solid fuel, waste fuel, petroleum industry, etc., can solve the problems of poor structural stability, low carbon content, and high ash content of briquette, and achieve improved molding stability and carbon content. The effect of high volume and surface tension reduction
- Summary
- Abstract
- Description
- Claims
- Application Information
AI Technical Summary
Problems solved by technology
Method used
Examples
preparation example Construction
[0037] The preparation method of briquette binding material A comprises the steps:
[0038](1) In parts by mass, take 7-13 parts of lithium-based grease, 2-5 parts of sodium-based bentonite, 1-3 parts of auxiliary materials, 3-7 parts of sodium aluminosilicate, 1-4 parts of dispersant, 4 ~8 parts of hydrogen-containing silicone oil, 30-50 parts of ethanol solution with a volume fraction of 70%, firstly take hydrogen-containing silicone oil, lithium-based grease, and auxiliary materials and mix them in a reactor, stir magnetically at 400-700r / min for 30-55min, add sodium Mix base bentonite, sodium aluminosilicate, dispersant, and ethanol solution, and shear and disperse at 2000~4000r / min for 15~25min to obtain a dispersion. At 28~36°C, add trimethyl Mix and stir the chlorosilane for 1~3h, filter with suction, collect the filter residue, wash it with water for 2~4 times, move it to a 65~80℃ oven and dry it for 1~3h to obtain the base material;
[0039] (2) Under a nitrogen atmo...
Embodiment 1
[0043] Dispersant: Mix sodium dodecylbenzenesulfonate and fatty alcohol polyoxyethylene ether at a mass ratio of 2:1 to obtain a dispersant.
[0044] Catalyst: Mix chloroplatinic acid and ferrocene at a mass ratio of 1:1 to obtain a catalyst.
[0045] Additive: Mix linseed oil and hydroxyapatite at a mass ratio of 1:3 to obtain the additive.
[0046] Auxiliary material: Mix polyacrylamide and hydroxyethyl cellulose at a mass ratio of 2:1 to obtain an auxiliary material.
[0047] Modifier: Mix β-cyclodextrin, microcrystalline paraffin, and lecithin at a mass ratio of 5:1:1 to obtain a modifier.
[0048] Pretreatment lignite: take lignite and crush it through a 60-mesh sieve, wash the sieved material twice with a sodium bicarbonate solution with a mass fraction of 15%, and dry it to obtain a dry product. Take the dry product and add it in a mass ratio of 7:5:1 Mix itaconic acid and acrylamide evenly, evaporate under reduced pressure to constant weight, and obtain pretreated li...
Embodiment 2
[0056] Dispersant: Mix sodium dodecylbenzenesulfonate and fatty alcohol polyoxyethylene ether at a mass ratio of 5:1 to obtain a dispersant.
[0057] Catalyst: Mix chloroplatinic acid and ferrocene in a mass ratio of 1:3 to obtain a catalyst.
[0058] Additive: Mix linseed oil and hydroxyapatite at a mass ratio of 1:6 to obtain the additive.
[0059] Auxiliary materials: Mix polyacrylamide and hydroxyethyl cellulose at a mass ratio of 5:1 to obtain auxiliary materials.
[0060] Modifier: Mix β-cyclodextrin, microcrystalline paraffin, and lecithin at a mass ratio of 8:1:2 to obtain a modifier.
[0061] Pretreatment lignite: take lignite and crush it through a 60-mesh sieve, take the sieved material and wash it with 15% sodium bicarbonate solution for 4 times, then dry it to obtain a dry product, take the dry product and add it according to the mass ratio of 13:5:1 Mix itaconic acid and acrylamide evenly, evaporate under reduced pressure to constant weight, and obtain pretreat...
PUM
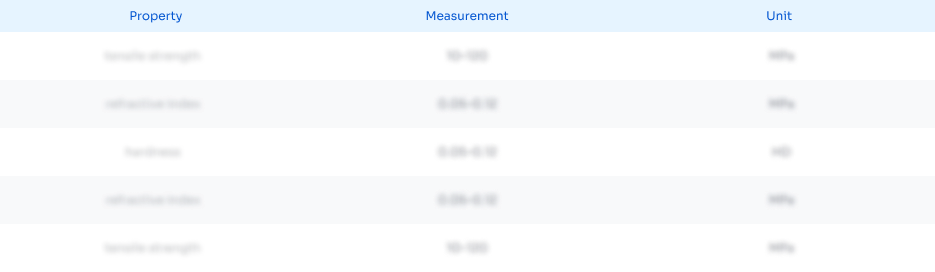
Abstract
Description
Claims
Application Information

- R&D
- Intellectual Property
- Life Sciences
- Materials
- Tech Scout
- Unparalleled Data Quality
- Higher Quality Content
- 60% Fewer Hallucinations
Browse by: Latest US Patents, China's latest patents, Technical Efficacy Thesaurus, Application Domain, Technology Topic, Popular Technical Reports.
© 2025 PatSnap. All rights reserved.Legal|Privacy policy|Modern Slavery Act Transparency Statement|Sitemap|About US| Contact US: help@patsnap.com