Method for separating aloe gel polysaccharide from aloe
A technology of aloe polysaccharide and aloe gel, which is applied in the field of separating aloe gelatin polysaccharide, can solve the problems of wasting aloe raw materials and solvents, high temperature, long time, etc., and achieves the advantages of saving wall breaking time, reducing losses, and short production cycle Effect
- Summary
- Abstract
- Description
- Claims
- Application Information
AI Technical Summary
Problems solved by technology
Method used
Examples
Embodiment 1
[0026] Cut 100.0g Aloe vera into slices of about 5mm, and dry it in vacuum at 30°C for 6 hours to obtain dried aloe, and then add 7g Na 2 CO 3 As an alkali aid, add balls at a filling rate of 10%, perform mechanical ball milling pretreatment at a speed of 500r / min for 30 minutes, and obtain dry aloe powder, then add a volume fraction of 10 at a material-to-liquid ratio of 1:15 % ethanol aqueous solution was used as the extraction solvent, ultrasonically extracted for 40 minutes at a temperature of 40°C, and 75% ethanol was added for precipitation to obtain 0.524 g of aloe polysaccharides, and the extraction rate of polysaccharides was 0.524%.
Embodiment 2
[0028] Cut 100.0g Aloe vera into thin slices of about 5mm, and dry it under vacuum for 8h at a temperature of 35°C to obtain dried aloe, and then add 8g Na 2 CO 3 As an alkali aid, add grinding balls at a filling rate of 15%, perform mechanical ball milling pretreatment at a speed of 400r / min for 25 minutes, and obtain dry aloe vera powder, then add 20% ethanol aqueous solution at a material-to-liquid ratio of 1:20 For the extraction solvent, ultrasonic extraction was performed at 45°C for 35 minutes, and 80% ethanol was added for precipitation to obtain 0.589 g of aloe polysaccharides, and the extraction rate of polysaccharides was 0.589%.
Embodiment 3
[0030] Cut 100.0g Aloe Vera into slices of about 5mm, and dry it under vacuum at 40°C for 10h to obtain dried Aloe Vera, then add 9g Na 2 CO 3 As an alkaline aid, add balls at a filling rate of 20%, perform mechanical ball milling pretreatment at a speed of 500r / min for 20 minutes, and obtain dry aloe vera powder, then add 25% ethanol aqueous solution at a material-to-liquid ratio of 1:25 For the extraction solvent, ultrasonic extraction was performed at 60°C for 40 minutes, and 90% ethanol was added for precipitation to obtain 0.612 g of aloe polysaccharides, and the extraction rate of polysaccharides was 0.612%.
PUM
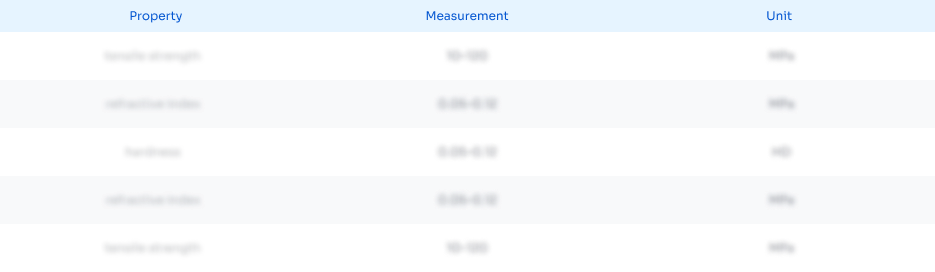
Abstract
Description
Claims
Application Information

- R&D
- Intellectual Property
- Life Sciences
- Materials
- Tech Scout
- Unparalleled Data Quality
- Higher Quality Content
- 60% Fewer Hallucinations
Browse by: Latest US Patents, China's latest patents, Technical Efficacy Thesaurus, Application Domain, Technology Topic, Popular Technical Reports.
© 2025 PatSnap. All rights reserved.Legal|Privacy policy|Modern Slavery Act Transparency Statement|Sitemap|About US| Contact US: help@patsnap.com