A self-calibration method of two-dimensional table error based on machine vision
A machine vision and workbench technology, applied in instruments, computer parts, image analysis, etc., can solve the problems of measurement accuracy, such as large influence, large influence, and high price of alignment error of line ruler, so as to improve the measurement accuracy. Efficiency, continuous dynamic measurement, the effect of reducing the amount of calculation
- Summary
- Abstract
- Description
- Claims
- Application Information
AI Technical Summary
Problems solved by technology
Method used
Image
Examples
Embodiment 1
[0054] S1 image acquisition steps: reset the image measuring instrument to zero, take the coins in a column along the X axis of the worktable and then focus, take the first picture im at the CCD camera coordinates (0,0,Z) 1 , the resolution of the picture is 1024 × 1280; then the CCD camera moves along the X axis for a distance of 5mm, and the CCD camera coordinates Y and Z values remain unchanged when moving along the X axis, the measurement range is 0-100mm, and a total of 21 pictures are obtained ; During the movement, the CCD camera does not focus repeatedly, and makes the picture taken at the current position overlap with the picture taken at the previous position by about 40%;
[0055] S2 image processing step: perform error compensation on the acquired image according to the aforementioned method, and complete the error self-calibration of the two-dimensional workbench;
[0056] S3 accuracy verification: to verify the accuracy of the two-dimensional workbench error de...
PUM
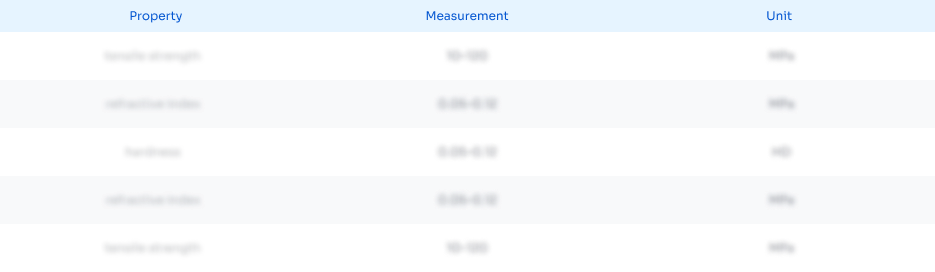
Abstract
Description
Claims
Application Information

- Generate Ideas
- Intellectual Property
- Life Sciences
- Materials
- Tech Scout
- Unparalleled Data Quality
- Higher Quality Content
- 60% Fewer Hallucinations
Browse by: Latest US Patents, China's latest patents, Technical Efficacy Thesaurus, Application Domain, Technology Topic, Popular Technical Reports.
© 2025 PatSnap. All rights reserved.Legal|Privacy policy|Modern Slavery Act Transparency Statement|Sitemap|About US| Contact US: help@patsnap.com