Preparation method of narrow-distribution polyacrylonitrile-based carbon fiber spinning solution
A polyacrylonitrile-based carbon fiber and spinning dope technology, which is applied in the chemical characteristics of fibers, textiles and papermaking, etc., can solve the problems of wide molecular weight distribution of polyacrylonitrile, long reaction time, high residual monomer content, and achieve polymerization reaction time. The effect of shortening, reducing residues, reducing half-life
- Summary
- Abstract
- Description
- Claims
- Application Information
AI Technical Summary
Problems solved by technology
Method used
Examples
Embodiment 1
[0031] 990 g of distilled acrylonitrile (AN), 5 g of itaconic acid (IA), 2.5 g of sodium methacrylate, 5 g of azobisisobutyronitrile (AIBN) and 3900 g of dimethylsulfoxide (DMSO) were added to Stir the reactor evenly, close the reactor, and start the constant temperature reaction under the protection of nitrogen under a slight positive pressure, and control the reaction temperature to 60°C. When the conversion rate reaches 70%, raise the temperature by 5°C to 65°C, and continue the reaction; when the conversion rate reaches 90%, raise the temperature by 5°C to 70°C, and continue the reaction; when the conversion rate reaches 95%, stop the polymerization, The total polymerization time was 22 hours. Start stripping for 8 hours, control the temperature at 70°C, and the pressure at 200Pa; let stand for defoaming for 12 hours, control the temperature at 75°C, and the pressure at 150Pa.
[0032] The molecular weight of the spinning stock solution is 70,000, the molecular weight dis...
Embodiment 2
[0034] 1210 g of distilled acrylonitrile (AN), 27.5 g of methyl methacrylate, 2 g of sodium propylene sulfonate, 7.5 g of azobisisobutyronitrile (AIBN) and 3760 g of dimethylsulfoxide (DMSO) were charged to the reactor , stir evenly, close the reactor, and start the constant temperature reaction under the protection of helium under a slight positive pressure, and control the reaction temperature to 65°C. When the conversion rate reaches 65%, raise the temperature by 5°C to 70°C, and continue the reaction; when the conversion rate reaches 85%, raise the temperature by 10°C to 80°C, and continue the reaction; when the conversion rate reaches 90%, stop the polymerization, The total polymerization time was 20 hours. Start stripping for 8 hours, control the temperature at 75°C, and the pressure at 300Pa; let stand for defoaming for 12 hours, control the temperature at 75°C, and the pressure at 200Pa.
[0035] The molecular weight of the spinning stock solution is 60,000, the molec...
Embodiment 3
[0037]Add 1460g of distilled acrylonitrile (AN), 30g of acrylamide, 15g of sodium methacrylate, 9g of azobisisobutyronitrile (AIBN) and 3500g of dimethyl sulfoxide (DMSO) into the reactor and stir evenly , close the reactor, start the constant temperature reaction under the protection of argon under a slight positive pressure, and control the reaction temperature to 62°C. When the conversion rate reaches 60%, raise the temperature by 10°C to 72°C, and continue the reaction; when the conversion rate reaches 80%, raise the temperature by 5°C to 77°C, and continue the reaction; when the conversion rate reaches 95%, stop the polymerization, The total polymerization time was 22 hours. Start stripping for 8 hours, control the temperature at 70°C, and the pressure at 100Pa; let stand for defoaming for 12 hours, control the temperature at 75°C, and the pressure at 100Pa.
[0038] The molecular weight of the spinning stock solution is 80,000, the molecular weight distribution is 3.7, ...
PUM
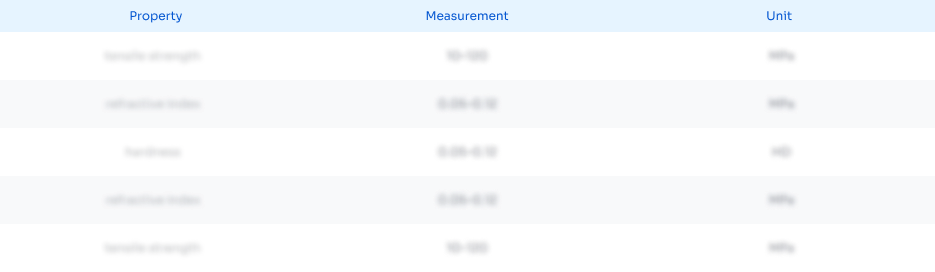
Abstract
Description
Claims
Application Information

- R&D
- Intellectual Property
- Life Sciences
- Materials
- Tech Scout
- Unparalleled Data Quality
- Higher Quality Content
- 60% Fewer Hallucinations
Browse by: Latest US Patents, China's latest patents, Technical Efficacy Thesaurus, Application Domain, Technology Topic, Popular Technical Reports.
© 2025 PatSnap. All rights reserved.Legal|Privacy policy|Modern Slavery Act Transparency Statement|Sitemap|About US| Contact US: help@patsnap.com