System and method for multiple pipeline ultrasonic non-destructive detection and automatic detection for three-dimensional modelling locating dead pixels
A non-destructive testing and 3D modeling technology, applied in the analysis of solids using sonic/ultrasonic/infrasonic waves, material analysis using sonic/ultrasonic/infrasonic waves, construction, etc. Location and other issues, to achieve the effect of high degree of automation, material saving, saving testing time
- Summary
- Abstract
- Description
- Claims
- Application Information
AI Technical Summary
Problems solved by technology
Method used
Image
Examples
Embodiment Construction
[0049] In order to have a further understanding and understanding of the structural features of the present invention and the achieved effects, the preferred embodiments and accompanying drawings are used for a detailed description, as follows:
[0050] The present invention implements a multi-pipeline ultrasonic nondestructive testing system, such as figure 1 The entire system shown includes a high-voltage pulse transmission module, a signal processing module, a probe lifting system, an ultrasonic probe, a depth counter, and a host. The whole system is controlled by the host computer. The signal processing module, the probe lifting system, and the depth counter are all interconnected with the host; at the same time, the host and the high-voltage pulse transmission module send control information in one direction; multiple ultrasonic probes are composed of ultrasonic transducers, and the ultrasonic transducers Connect with the high-voltage pulse transmission module and the si...
PUM
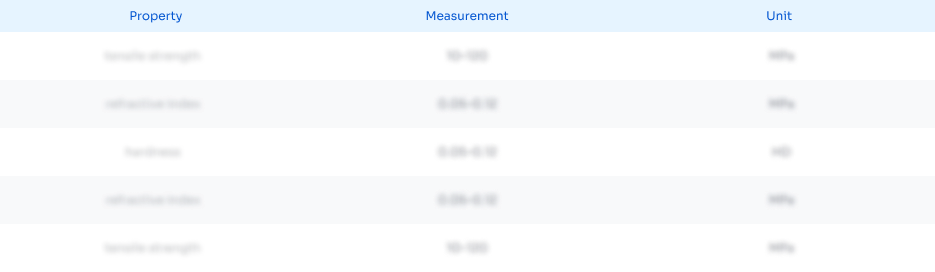
Abstract
Description
Claims
Application Information

- R&D Engineer
- R&D Manager
- IP Professional
- Industry Leading Data Capabilities
- Powerful AI technology
- Patent DNA Extraction
Browse by: Latest US Patents, China's latest patents, Technical Efficacy Thesaurus, Application Domain, Technology Topic, Popular Technical Reports.
© 2024 PatSnap. All rights reserved.Legal|Privacy policy|Modern Slavery Act Transparency Statement|Sitemap|About US| Contact US: help@patsnap.com