A kind of preparation method of porous nanometer silicon carbon composite material
A carbon composite material and nano-silicon technology, which is applied in the preparation/purification of carbon, silicon compounds, chemical instruments and methods, etc., can solve the problems of complex process, risk of explosion, poor charge and discharge performance, etc., and achieve low preparation cost and no The effect of environmental pollution and simple process
- Summary
- Abstract
- Description
- Claims
- Application Information
AI Technical Summary
Problems solved by technology
Method used
Image
Examples
Embodiment 1
[0035] A method for preparing a porous nano-silicon-carbon composite material, comprising the steps of:
[0036] Step 1, put raw talc powder into a corundum crucible, and then put it into a tube furnace for calcination. The process of calcining raw talc powder is as follows: the heating rate is 4°C / min, the holding temperature is 700°C, and the holding time is 100 minutes. Cool down to 300°C at a cooling rate of 15°C / min and then cool with the furnace to obtain calcined talc powder D1;
[0037] Step 2, fully mix the D1 prepared in step 1 according to the mass ratio of D1 and magnesium powder of 1:1, and use dry pressing to form at 50MPa, hold the pressure for 10min and press it into a block to obtain the mixed block material MD1;
[0038] Step 3, put the MD1 prepared in step 2 into a corundum crucible, and calcine it in six stages in a tube furnace, which are: the first stage—rising from room temperature to 600°C, the second stage—in 600 ° C for 3 hours, the third stage - aft...
Embodiment 2
[0042] A method for preparing a porous nano-silicon-carbon composite material, comprising the steps of:
[0043] Step 1, put raw talc powder into a corundum crucible, and then put it into a tube furnace for calcination. The process of calcining raw talc powder is as follows: the heating rate is 5°C / min, the holding temperature is 720°C, and the holding time is 90 minutes. Reduce the temperature to 300°C at a cooling rate of 4°C / min and then cool with the furnace to obtain calcined talc powder D1;
[0044] Step 2, fully mix the D1 prepared in step 1 according to the mass ratio of D1 and magnesium powder of 1:3, and use dry pressing at 200MPa, hold the pressure for 3min and press into a block to obtain the mixed block material MD1;
[0045]Step 3, put the MD1 prepared in step 2 into a corundum crucible, and calcine it in six stages in a tube furnace, which are: the first stage—rising from room temperature to 620°C, the second stage—in 620°C heat preservation for 2.5h, the third...
Embodiment 3
[0049] A method for preparing a porous nano-silicon-carbon composite material, comprising the steps of:
[0050] Step 1, put raw talc powder into a corundum crucible, and then put it into a tube furnace for calcination. The process of calcining raw talc powder is as follows: the heating rate is 4°C / min, the holding temperature is 680°C, and the holding time is 150 minutes. Reduce the temperature to 300°C at a cooling rate of 4°C / min and then cool with the furnace to obtain calcined talc powder D1;
[0051] Step 2, fully mix the D1 prepared in step 1 according to the mass ratio of D1 and magnesium powder of 1:1.5, and use dry pressing to form a block at 100MPa, hold the pressure for 5 minutes, and press it into a block to obtain the mixed block material MD1;
[0052] Step 3, put the MD1 prepared in step 2 into a corundum crucible, and calcine it in six stages in a tube furnace, which are: the first stage—rising from room temperature to 630°C, the second stage—in 630°C for 2 ho...
PUM
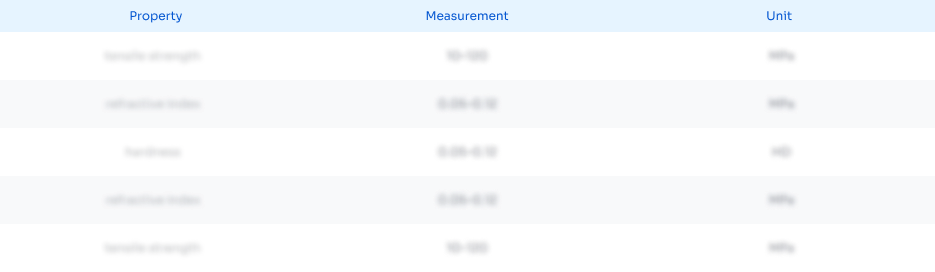
Abstract
Description
Claims
Application Information

- R&D Engineer
- R&D Manager
- IP Professional
- Industry Leading Data Capabilities
- Powerful AI technology
- Patent DNA Extraction
Browse by: Latest US Patents, China's latest patents, Technical Efficacy Thesaurus, Application Domain, Technology Topic, Popular Technical Reports.
© 2024 PatSnap. All rights reserved.Legal|Privacy policy|Modern Slavery Act Transparency Statement|Sitemap|About US| Contact US: help@patsnap.com