Manufacturing process of polyphenylene sulfide film
A technology of polyphenylene sulfide film and manufacturing process, which is applied in the field of polyphenylene sulfide film manufacturing process, and can solve the problems of complex film production process and process conditions
- Summary
- Abstract
- Description
- Claims
- Application Information
AI Technical Summary
Problems solved by technology
Method used
Image
Examples
Embodiment 1
[0046] First, sodium hydrosulfide and sodium hydroxide are added to N-methyl-2-pyrrolidone solvent, and then oxygen-free deionized water of 9 mol / mol NaHS is added to make NaHS in the system: NaOH: NMP: H 2 The molar ratio of O is 1.0:1.16:1.5:10.0; heated to 148°C at a heating rate of 2.0°C / min, kept at this temperature for 1.5h, and then heated to 183°C at a heating rate of 1.0°C / min. Insulate for 1.5 hours, then raise the temperature to 213°C. Under this temperature condition, keep hold for 8 minutes, and then drop the temperature to 203°C. After the system materials are processed by such a treatment process, the Na in the system 2 S:NMP:H 2 The mol ratio of O is 1.0: 0.6: 1.1; Add p-dichlorobenzene, hexachlorobenzene raw material and NMP solvent again, make the Na of the system 2 S:p-DCB:Hexachlorobenzene:NMP:H 2 The molar ratio of O is 1.0: 0.98: 0.13: 3.3: 1.1; then the temperature of the system is raised to 218°C. Under this temperature condition, after 4.5h of heat p...
Embodiment 2
[0051] First, sodium hydrosulfide and sodium hydroxide are added to the N-methyl-2-pyrrolidone solvent, and then 11mol / mol NaHS oxygen-free deionized water is added to make the NaHS in the system: NaOH: NMP: H 2 The molar ratio of O is 1.0:1.19:1.8:12.0; heated to 158°C at a heating rate of 3.0°C / min, kept at this temperature for 1.0h, and then heated to 188°C at a heating rate of 2.0°C / min. Keep warm for 1.0h, and then raise the temperature to 233°C. Under this temperature condition, keep warm for 3 minutes, and then drop the temperature to 206°C. After the system materials are processed by such a treatment process, the Na in the system 2 S:NMP:H 2 The mol ratio of O is 1.0: 0.9: 1.8; Add p-dichlorobenzene, hexachlorobenzene raw material and NMP solvent again, make the Na of the system 2 S:p-DCB:Hexachlorobenzene:NMP:H 2 The molar ratio of O is 1.0:0.99:0.18:3.3~3.8:1.8; then the temperature of the system is raised to 222°C. Under this temperature condition, after 3.0 hours...
Embodiment 3
[0061] First, sodium hydrosulfide and sodium hydroxide are added to the N-methyl-2-pyrrolidone solvent, and then 10mol / mol NaHS oxygen-free deionized water is added to make the NaHS in the system: NaOH: NMP: H 2 The molar ratio of O is 1.0:1.17:1.6:11.0; heated to 151°C at a heating rate of 2.3°C / min, kept at this temperature for 1.2h, and then heated to 184°C at a heating rate of 1.3°C / min. Insulate for 1.4 hours, then raise the temperature to 225°C. Under this temperature condition, keep hold for 6 minutes, and then drop the temperature to 204°C. After the system materials are processed by such a treatment process, the Na in the system 2 S:NMP:H 2 The mol ratio of O is 1.0: 0.7: 1.4; Add p-dichlorobenzene, hexachlorobenzene raw material and NMP solvent again, make the Na of the system 2 S:p-DCB:Hexachlorobenzene:NMP:H 2 The molar ratio of O is 1.0: 0.983: 0.143: 3.5: 1.4; then the temperature of the system is raised to 220°C. Under this temperature condition, after 3.5 hou...
PUM
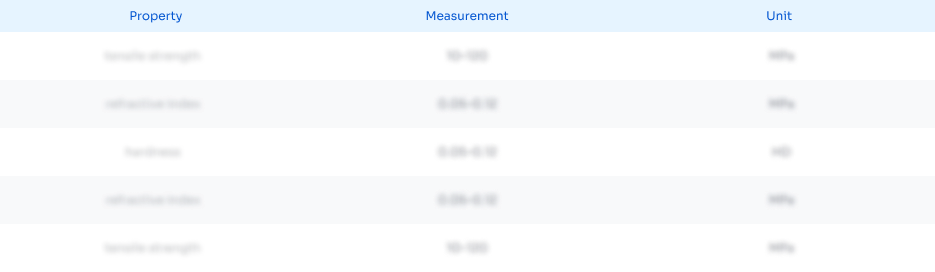
Abstract
Description
Claims
Application Information

- R&D Engineer
- R&D Manager
- IP Professional
- Industry Leading Data Capabilities
- Powerful AI technology
- Patent DNA Extraction
Browse by: Latest US Patents, China's latest patents, Technical Efficacy Thesaurus, Application Domain, Technology Topic, Popular Technical Reports.
© 2024 PatSnap. All rights reserved.Legal|Privacy policy|Modern Slavery Act Transparency Statement|Sitemap|About US| Contact US: help@patsnap.com