A kind of vacuum degreasing sintering furnace and using method thereof
A vacuum degreasing and sintering furnace technology, applied in furnaces, furnace types, lighting and heating equipment, etc., can solve problems such as prolonging degreasing time, speeding up degreasing speed, and binder pollution, improving performance and quality, and reducing the degree of pollution. , the effect of prolonging the service life
- Summary
- Abstract
- Description
- Claims
- Application Information
AI Technical Summary
Problems solved by technology
Method used
Image
Examples
Embodiment 1
[0051] Such as Figure 4-Figure 5 As shown: this embodiment provides a vacuum degreasing sintering furnace, including a furnace body 1 and a carbon fiber heat insulation cylinder 2 arranged inside the furnace body 1, and a graphite material box 3 is arranged inside the carbon fiber heat insulation cylinder 2, and the graphite material box 3 A material box loam cake 24 is provided in the middle of the upper side. There are several graphite heating rods 21 evenly distributed along the circumferential direction between the carbon fiber heat insulating cylinder 2 and the graphite material box 3, and several thermocouples 22 are respectively arranged on the upper side and the lower side of the graphite material box 3, and the thermocouples 22 are respectively used to detect graphite materials. The temperature of the upper and lower sides of box 3.
[0052] The graphite material box 3 is provided with an inner gas filling port 4 and an inner gas extraction port 5, and the inner gas...
Embodiment 2
[0058] Such as Image 6 Shown: The difference between this embodiment and Embodiment 1 is that: the inner gas filling port 4 is arranged in the middle of the upper side of the graphite material box 3, the inner air extraction port 5 is arranged at the two ends of the lower side of the graphite material box 3, and the two rows of material plates 13 Adjacent ends are respectively provided with a gas guiding device 12 , the upper cover 24 of the material box is arranged on the two ends of the upper side of the graphite material box 3 , and the outer air extraction port 9 is arranged on the lower side of the furnace body 1 . For other technical features and usage methods, please refer to Embodiment 1.
Embodiment 3
[0060] Such as Figure 7 Shown: The difference between this embodiment and Embodiment 1 is that: the inner gas filling port 4 is arranged on one end of the upper side of the graphite material box 3, such as the right end, and the inner air extraction port 5 is arranged on the other end of the lower side of the graphite material box 3, such as the left end , The material plate 13 is provided in multiple layers, only the right end of the material plate 13 is provided with the air guiding device 12, and the outer air extraction port 9 is arranged on the lower side of the furnace body 1. For other technical features and usage methods, please refer to Embodiment 1.
PUM
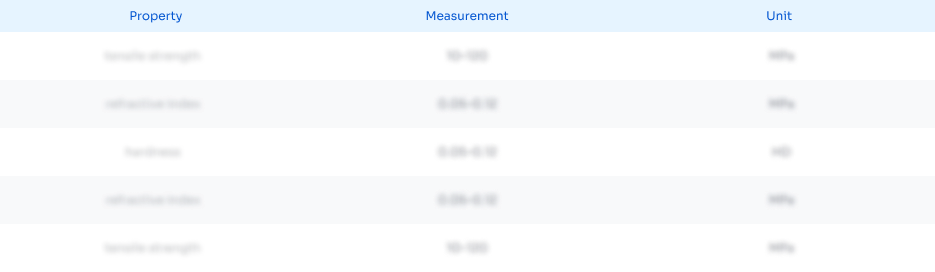
Abstract
Description
Claims
Application Information

- R&D Engineer
- R&D Manager
- IP Professional
- Industry Leading Data Capabilities
- Powerful AI technology
- Patent DNA Extraction
Browse by: Latest US Patents, China's latest patents, Technical Efficacy Thesaurus, Application Domain, Technology Topic, Popular Technical Reports.
© 2024 PatSnap. All rights reserved.Legal|Privacy policy|Modern Slavery Act Transparency Statement|Sitemap|About US| Contact US: help@patsnap.com