Reconstituted tobacco leaf suitable for heat-not-burn cigarettes and its improved dry preparation method
A heat-not-burn and reconstituted tobacco leaf technology, applied in the preparation of tobacco, tobacco, application, etc., can solve the problems of low tightness, concentration, fullness, fullness, agglomeration, lack of thickness, bulkiness, air permeability, Problems such as high porosity, to achieve the effects of increased tensile strength, enhanced machine adaptability, and enhanced sense of thickness
- Summary
- Abstract
- Description
- Claims
- Application Information
AI Technical Summary
Problems solved by technology
Method used
Image
Examples
Embodiment 1
[0041] The defibrated coniferous wood pulp and flax pulp are mixed according to the mass ratio of 9:1, and the dry-laid film base is prepared after air-flow forming at the forming head, and the basis weight is 20g / m 2 , the bulk thickness is 6cm 3 / g. According to product design requirements and formula requirements, the coating liquid for coating is prepared. The formula of the coating liquid is: by weight, 10 parts of tobacco particles (200 mesh), 4 parts of smoking agent, 4 parts of adhesive, tobacco extract 3 parts of substance, 2 parts of dispersant, 3 parts of food additive, 2 parts of essence for tobacco, 80 parts of water, the solid content of the coating liquid is 10%, and the viscosity is 355mPa·s. According to attached figure 1 In the process flow shown, the prepared coating solution is sprayed four times (each spraying amount is 25g / m 2 ), one curtain coating (spraying amount is 30g / m 2 ) is transferred to the sheet base and the surface of the coated substrate ...
Embodiment 2
[0043] The defibrated coniferous wood pulp, tobacco stem pulp, and tobacco stem pulp were mixed according to the mass ratio of 6:1:3, and air-flow formed by the forming head to prepare a dry-laid sheet base, with a weight of 40g / m 2 , the bulk thickness is 4.8cm 3 / g. Prepare coating liquid for coating according to product design requirements and formula requirements, the formula of coating liquid is: by weight, 15 parts of tobacco particles (200 mesh), 6 parts of smoking agent, 5 parts of adhesive, tobacco extract 4 parts of substance, 2 parts of dispersant, 3 parts of food additive, 2 parts of essence for tobacco, 85 parts of water, the solid content of the coating liquid is 12%, and the viscosity is 860mPa·s. According to attached figure 2 As shown in the process flow, the prepared coating liquid is sprayed three times (each spraying amount is 25g / m 2 ), one curtain coating (spraying amount is 30g / m 2 ) to the surface and interior of the sheet base to obtain semi-finis...
Embodiment 3
[0045] The defibrated coniferous wood pulp and bamboo pulp are mixed according to the mass ratio of 7:3, and the dry-laid film base is prepared after air-flow forming at the forming head, and the basis weight is 60g / m 2 , the bulk thickness is 7cm 3 / g. Prepare coating liquid for coating according to product design requirements and formula requirements, the formula of coating liquid is: by weight, 20 parts of tobacco particles (200 mesh), 8 parts of smoking agent, 6 parts of adhesive, tobacco 5 parts of extract, 3 parts of dispersant, 4 parts of food additive, 3 parts of essence for tobacco, 90 parts of water, the solid content of the coating liquid is 13%, and the viscosity is 930mPa·s. According to attached image 3 As shown in the process flow, the prepared coating solution is sprayed twice (each spraying amount is 25g / m 2 ), two curtain coatings (each spraying amount is 30g / m 2 ) to the surface and interior of the sheet base to obtain semi-finished reconstituted tobacc...
PUM
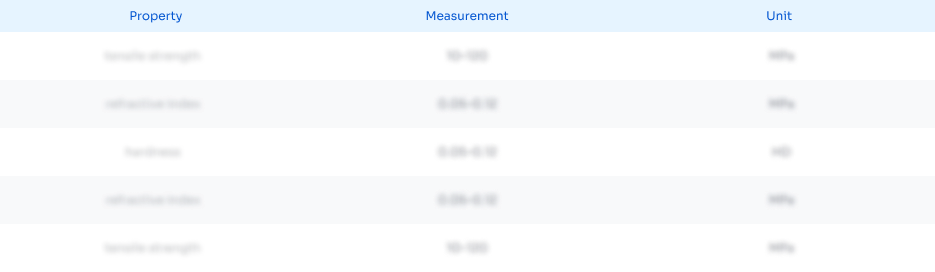
Abstract
Description
Claims
Application Information

- R&D
- Intellectual Property
- Life Sciences
- Materials
- Tech Scout
- Unparalleled Data Quality
- Higher Quality Content
- 60% Fewer Hallucinations
Browse by: Latest US Patents, China's latest patents, Technical Efficacy Thesaurus, Application Domain, Technology Topic, Popular Technical Reports.
© 2025 PatSnap. All rights reserved.Legal|Privacy policy|Modern Slavery Act Transparency Statement|Sitemap|About US| Contact US: help@patsnap.com