High-performance polyurethane damping material and one-step production method thereof
A damping material, polyurethane technology, applied in the field of polyurethane, can solve the problems of increased viscosity of the material system, uneven damping performance, uneven dispersion of fillers, etc., to achieve high elongation, good wear resistance, and a large adjustable range of hardness Effect
- Summary
- Abstract
- Description
- Claims
- Application Information
AI Technical Summary
Problems solved by technology
Method used
Image
Examples
Embodiment 1
[0025] (1) Dehydration of polyols: Dehydrate 400 g of polycaprolactone diols with a number-average molecular weight of 2000 at 95-100° C. for 2 hours under a vacuum of -0.1 MPa.
[0026] (2) Preparation of elastomer: polycaprolactone diol, chain extender 1 and catalyst (using propylene glycol to prepare triethylenediamine content as 33% solution) with number average molecular weight of 2000 after dehydration, according to Proportion 100g / 26.6g / 0.05g After mixing evenly, keep the temperature at 70°C, add 40g of MDI, mix evenly and defoam, pour into a mold at 120°C, demould for 60 minutes, vulcanize for 20 hours at 100°C, and measure after 7 days at room temperature performance. The properties of the obtained materials are shown in Table 2.
Embodiment 2
[0028] (1) Dehydration of polyols: 400 g of polycaprolactone diols with a number average molecular weight of 1000 are dehydrated at 95 to 100 ° C for 2 hours under a vacuum degree of -0.1 MPa, and are discharged for later use; 400 g of polycaprolactone diols with a number average molecular weight of 550 Caprolactone trihydric alcohol is dehydrated at 95-100°C and vacuum degree -0.1MPa for 2 hours, and the material is discharged for later use;
[0029] (2) Preparation of elastomer: polycaprolactone dibasic alcohol after dehydration, polycaprolactone tribasic alcohol, chain extender 2, catalyst (use the triethylenediamine content of propylene glycol preparation to be the solution of 33%) ) according to the ratio of 100 / 31.2 / 19.7 / 0.08, mix evenly, keep the temperature at 70°C, add 55g of MDI, mix evenly and defoam, pour it into a mold at 120°C, demould after 120min, vulcanize at 100°C for 20h, and place it at room temperature Performance was measured after 7 days. The properties...
Embodiment 3
[0031] (1) Dehydration of polyols: 400 g of polytetrahydrofuran diols with a number-average molecular weight of 2000 were dehydrated for 2 hours at 95-100° C. and a vacuum degree of -0.1 MPa, and discharged for later use.
[0032] (2) Preparation of elastomer: mix polytetrahydrofuran diol with a number average molecular weight of 2000 after dehydration, chain extender 1, and catalyst T-12 in a proportion of 100g / / 13.8g / 0.0g8, and keep the temperature at 80°C , add 18.5g TDI, mix evenly and defoam, pour it into a mold at 120°C, demould after 120min, vulcanize at 100°C for 24h, leave it at room temperature for 7 days, then test its performance. The properties of the obtained materials are shown in Table 2.
PUM
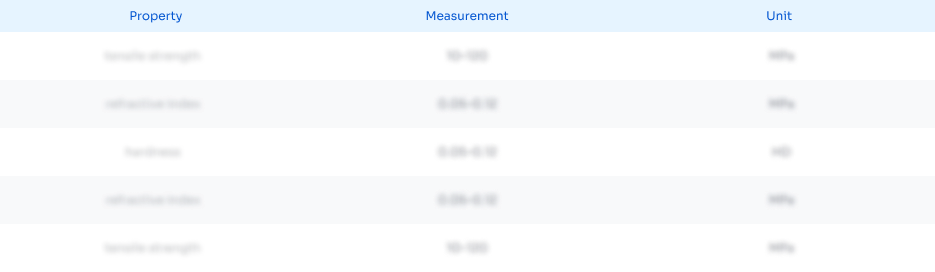
Abstract
Description
Claims
Application Information

- R&D
- Intellectual Property
- Life Sciences
- Materials
- Tech Scout
- Unparalleled Data Quality
- Higher Quality Content
- 60% Fewer Hallucinations
Browse by: Latest US Patents, China's latest patents, Technical Efficacy Thesaurus, Application Domain, Technology Topic, Popular Technical Reports.
© 2025 PatSnap. All rights reserved.Legal|Privacy policy|Modern Slavery Act Transparency Statement|Sitemap|About US| Contact US: help@patsnap.com