High temperature resistant and low compression permanent deformation ethylene propylene diene monomer and preparation method thereof
A technology of EPDM rubber and low-pressure change, which is applied in the field of EPDM rubber and its preparation, can solve the problems of poor high temperature resistance and compression set performance, and difficulty in meeting the use requirements, so as to improve flame resistance and high temperature Compression set performance and high temperature aging resistance, anti-aging effect
- Summary
- Abstract
- Description
- Claims
- Application Information
AI Technical Summary
Problems solved by technology
Method used
Image
Examples
Embodiment 1
[0023] S1. Kneading: knead 100g EPDM raw rubber, 20g neoprene, and 0.6g zinc stearate in a vacuum kneader for 3-5 minutes, first add 30g graphene to the organic solvent tetrahydrofuran, and ultrasonically 5min to form a uniform and stable dispersion, then add the dispersion to the kneaded silica gel, continue ultrasonic stirring, the raw rubber mixture will gather into the graphene oxide sheet structure in the form of intercalation, and the solvent molecules will continue to desorb in the form of Ensure the entropy balance of the system, finally form a stable intercalation structure, remove the solvent by rotary evaporation to obtain a graphene / rubber composite material, add 0.2g BaSO in 3-4 times 4 , 50g carbon black N990, 5g zinc oxide, 0.1g 2-mercaptobenzimidazole, 0.2g dioctyl adipate, 0.1g carnauba wax, stir and mix at 10-50 rpm Heat treatment for 10-30min under certain conditions, then vacuumize at -0.07- -0.05Mpa, after vacuuming for 30-60 minutes, the glue will come ou...
Embodiment 2
[0027] S1. Kneading: knead 100g EPDM raw rubber, 30g chloroprene rubber, and 3g zinc stearate in a vacuum kneader for 3-5 minutes, first add 50g graphene to the organic solvent tetrahydrofuran, and ultrasonicate for 5 minutes Form a uniform and stable dispersion, then add the dispersion to the kneaded silica gel, continue to stir ultrasonically, the raw rubber mixture will gather into the graphene oxide sheet structure in the form of intercalation, and the solvent molecules will continue to be desorbed to ensure The entropy balance of the system finally forms a stable intercalation structure, and the solvent is removed by rotary evaporation to obtain a graphene / rubber composite material. Add 0.8g BaSO4, 40g carbon black N990, 40g glass beads, 10g zinc oxide, 0.2g 2-mercaptobenzimidazole, 0.4g dioctyl adipate, 0.4g carnauba wax, stir and mix at 10-50 rpm, heat treatment at 60-90°C for 10-30min, and then vacuum -0.07- -0.05Mpa, after vacuuming for 30-60 minutes, the glue will co...
Embodiment 3
[0031] S1. Kneading: Knead 100g EPDM raw rubber, 25g neoprene rubber, and 1g zinc stearate in a vacuum kneader for 3-5 minutes, first add 40g graphene to the organic solvent tetrahydrofuran, and ultrasonicate for 5 minutes Form a uniform and stable dispersion, then add the dispersion to the kneaded silica gel, continue to stir ultrasonically, the raw rubber mixture will gather into the graphene oxide sheet structure in the form of intercalation, and the solvent molecules will continue to be desorbed to ensure The entropy balance of the system finally forms a stable intercalation structure, and the solvent is removed by rotary evaporation to obtain a graphene / rubber composite material. Add 0.6g BaSO4, 60g carbon black N990, 8g zinc oxide, 0.2g 2-mercaptobenzene in 3-4 times Imimidazole, 0.2g dioctyl adipate, 0.2g carnauba wax, stir and mix evenly at 10-50 rpm, heat treatment at 60-90°C for 10-30min, and then vacuumize to -0.07- -0.05Mpa, after vacuuming for 30-60 minutes, the g...
PUM
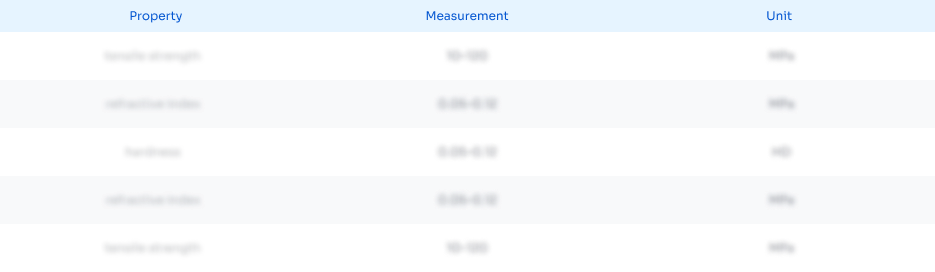
Abstract
Description
Claims
Application Information

- R&D
- Intellectual Property
- Life Sciences
- Materials
- Tech Scout
- Unparalleled Data Quality
- Higher Quality Content
- 60% Fewer Hallucinations
Browse by: Latest US Patents, China's latest patents, Technical Efficacy Thesaurus, Application Domain, Technology Topic, Popular Technical Reports.
© 2025 PatSnap. All rights reserved.Legal|Privacy policy|Modern Slavery Act Transparency Statement|Sitemap|About US| Contact US: help@patsnap.com