Production method of bimetal composite hob ring
A production method and bimetal technology, applied in the production field of bimetal composite hob cutter ring, can solve the problems of incapable of simultaneous improvement, high machining accuracy, and high use cost, and achieve increased interface bonding area, improved usability, and improved use. effect of life
- Summary
- Abstract
- Description
- Claims
- Application Information
AI Technical Summary
Problems solved by technology
Method used
Examples
Embodiment 1
[0019] Embodiment 1, taking the composite molding of a 17-inch hob cutter ring in a vertical centrifuge as an example,
[0020] First of all, the material required for the outer ring of the hob cutter is smelted into liquid steel in an electroslag crucible furnace. The outer ring of the hob cutter needs wear resistance, so it needs to have high wear resistance. For this reason, in In this embodiment, high wear-resistant stainless steel is selected. In this embodiment, a wear-resistant alloy material with a hardness above HRC60 is selected. Specifically, the alloy tool steel with high wear resistance is any of Cr12MoV, 3Cr2W8V, 4Cr5MoSiV1 or LD. One material, in this example, is 4Cr5MoSiV1.
[0021] The inner ring of the hob cutter ring needs a certain degree of toughness. Therefore, the material of the inner ring of the hob cutter ring is high-toughness alloy steel. Of course, existing commonly used materials can also be selected. It is preferably any one of 42CrMo, 35CrMo, 4...
PUM
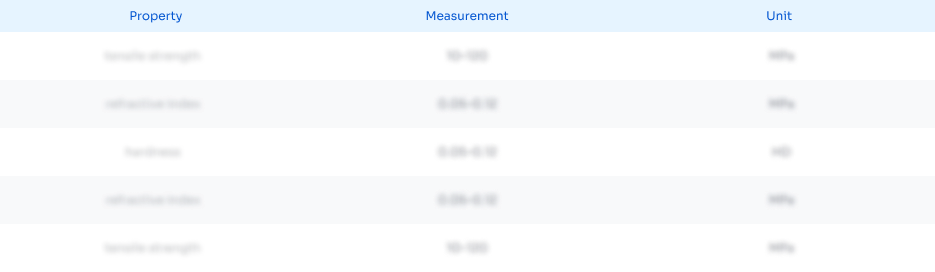
Abstract
Description
Claims
Application Information

- Generate Ideas
- Intellectual Property
- Life Sciences
- Materials
- Tech Scout
- Unparalleled Data Quality
- Higher Quality Content
- 60% Fewer Hallucinations
Browse by: Latest US Patents, China's latest patents, Technical Efficacy Thesaurus, Application Domain, Technology Topic, Popular Technical Reports.
© 2025 PatSnap. All rights reserved.Legal|Privacy policy|Modern Slavery Act Transparency Statement|Sitemap|About US| Contact US: help@patsnap.com