Method for producing continuous vulcanized fiber paper
A production method and technology of steel paper, which is applied in the field of papermaking, can solve problems such as insufficient bonding and delamination between steel paper layers, and achieve the effects of ensuring the effect of gelling treatment, improving production efficiency, and uniform cellulose reaction
- Summary
- Abstract
- Description
- Claims
- Application Information
AI Technical Summary
Problems solved by technology
Method used
Image
Examples
Embodiment 1
[0037] The embodiment is basically as figure 1 Shown: a kind of production method of continuous steel paper, comprises the following steps:
[0038] Step 1): Grinding and dispersing the finished plant fiber pulp by means of a pulverizer to loosen the plant fiber pulp.
[0039] Step 2): Send the loose plant fiber pulp to the zinc chloride solution spraying device, spray the zinc chloride solution, and carry out solid-liquid stirring for 20-40 minutes to carry out gelling treatment. In this embodiment, the stirring time is selected as 30min. In addition, the concentrated zinc chloride solution with a specific gravity of 1.91-1.98 is selected as the zinc chloride solution, and the concentrated zinc chloride solution with a specific gravity of 1.95 is selected in this embodiment.
[0040] Step 3): The gelatinized plant fibers are pulped and pressed by a pulp forming device to form continuous steel paper blanks, which are transported to the next process by paper guide rollers. S...
Embodiment 2
[0054] The differences between this embodiment and Embodiment 1 are:
[0055] The pulverizer adopted in the step 1), combined with figure 2 and image 3 As shown, two crushing rollers 1 rotating in the same direction are arranged inside, and lug plates 2 are arranged on the circumferential walls at both ends of each crushing roller 1. The axes of the rollers 1 are parallel, and the rotating shafts 3 are fixedly connected with crushing knives 4 , the crushing knives 4 on adjacent rotating shafts 3 are arranged alternately, and the crushing knives 4 on the two crushing rollers 1 are arranged alternately. A torsion spring 5 is arranged between the rotating shaft 3 and the ear plate 2 , one end of the torsion spring 5 is welded to the rotating shaft 3 , and the other end of the torsion spring 5 is welded to the ear plate 2 .
[0056] Both ends of the rotating shaft 3 are set through the ear plate 2, and the end of the rotating shaft 3 is welded with a baffle 6, which is paralle...
PUM
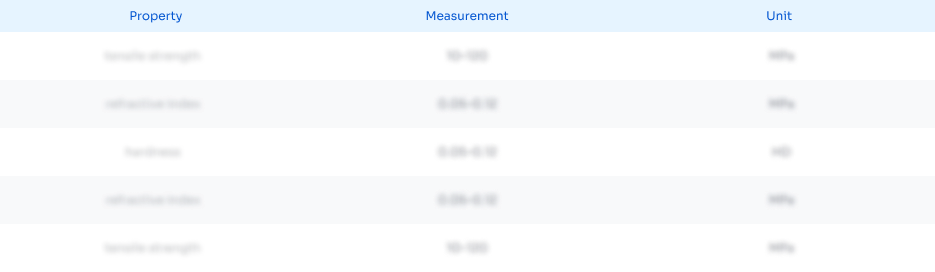
Abstract
Description
Claims
Application Information

- R&D
- Intellectual Property
- Life Sciences
- Materials
- Tech Scout
- Unparalleled Data Quality
- Higher Quality Content
- 60% Fewer Hallucinations
Browse by: Latest US Patents, China's latest patents, Technical Efficacy Thesaurus, Application Domain, Technology Topic, Popular Technical Reports.
© 2025 PatSnap. All rights reserved.Legal|Privacy policy|Modern Slavery Act Transparency Statement|Sitemap|About US| Contact US: help@patsnap.com