Shrink-proof printing process for wool fabrics
A printing process and fabric technology, applied in the field of fabric processing, can solve the problems of affecting the wettability of wool surface, the color of wool fabric is not bright enough, hindering the adsorption and diffusion of dyes, etc., to achieve bright colors, improve felt shrinkage, and color depth suitable effect
- Summary
- Abstract
- Description
- Claims
- Application Information
AI Technical Summary
Problems solved by technology
Method used
Examples
Embodiment 1
[0023] A shrink-proof printing process for wool fabrics, comprising the following steps:
[0024] (1) Ultrasonic cooking pre-treatment: put the woolen fabric in distilled water at 100°C, and perform alternating ultrasonic treatment with high, medium and low frequency ultrasonic waves, first with medium frequency ultrasonic for 3 minutes, then with low frequency ultrasonic for 6 minutes, then with medium frequency ultrasonic for 3 minutes, and then After 2 minutes of high-frequency ultrasonication, the decocting treatment is completed, and after the natural cooling to room temperature, ultrasonic cleaning is performed, and biological enzymes and neutral detergents are added. The amount of biological enzymes is 2g / L, the amount of neutral detergent is 15g / L, and the pH is adjusted to 5.0, low-frequency ultrasound for 8 minutes; wherein, the frequency of low-frequency ultrasound is 25Hz; the frequency of high-frequency ultrasound is 130Hz; the frequency of medium-frequency ultraso...
Embodiment 2
[0032] A shrink-proof printing process for wool fabrics, comprising the following steps:
[0033] (1) Ultrasonic cooking pretreatment: put the woolen fabric in distilled water at 110°C, and perform alternating ultrasonic treatment with high, medium and low frequency ultrasonic waves, first with medium frequency ultrasonic for 3 minutes, then with low frequency ultrasonic for 6 minutes, then with medium frequency ultrasonic for 3 minutes, and then After 2 minutes of high-frequency ultrasonication, the decocting treatment is completed, and after the natural cooling to room temperature, ultrasonic cleaning is performed, and biological enzymes and neutral detergents are added. The amount of biological enzymes is 2g / L, the amount of neutral detergent is 15g / L, and the pH is adjusted to 5.0, low-frequency ultrasound for 8 minutes; wherein, the frequency of low-frequency ultrasound is 25Hz; the frequency of high-frequency ultrasound is 130Hz; the frequency of medium-frequency ultrasou...
Embodiment 3
[0041] A shrink-proof printing process for wool fabrics, comprising the following steps:
[0042] (1) Ultrasonic cooking pre-treatment: put the wool fabric in distilled water at 105°C, and use high, medium and low frequency ultrasonic waves for alternating ultrasonic treatment. First, the medium frequency ultrasonic wave is 3 minutes, then the low frequency ultrasonic wave is used for 6 minutes, and then the medium frequency ultrasonic wave is used for 3 minutes. After 2 minutes of high-frequency ultrasonication, the decocting treatment is completed, and after the natural cooling to room temperature, ultrasonic cleaning is performed, and biological enzymes and neutral detergents are added. The amount of biological enzymes is 2g / L, the amount of neutral detergent is 15g / L, and the pH is adjusted to 5.0, low-frequency ultrasound for 8 minutes; wherein, the frequency of low-frequency ultrasound is 25Hz; the frequency of high-frequency ultrasound is 130Hz; the frequency of medium-f...
PUM
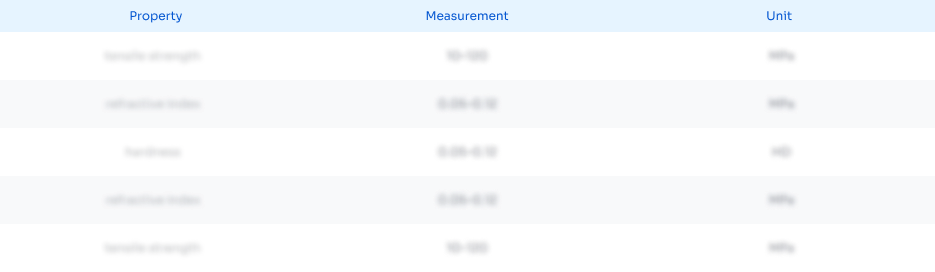
Abstract
Description
Claims
Application Information

- R&D
- Intellectual Property
- Life Sciences
- Materials
- Tech Scout
- Unparalleled Data Quality
- Higher Quality Content
- 60% Fewer Hallucinations
Browse by: Latest US Patents, China's latest patents, Technical Efficacy Thesaurus, Application Domain, Technology Topic, Popular Technical Reports.
© 2025 PatSnap. All rights reserved.Legal|Privacy policy|Modern Slavery Act Transparency Statement|Sitemap|About US| Contact US: help@patsnap.com