Photothermal double-cured resin composition for pultrusion and glass fiber composite material prepared from photothermal double-cured resin composition
A resin composition and dual curing technology, applied in the field of polymer materials, can solve the problems of low production efficiency, long curing time, environmental pollution, etc., and achieve the effects of high utilization rate, fast light curing speed and high mechanical strength
- Summary
- Abstract
- Description
- Claims
- Application Information
AI Technical Summary
Problems solved by technology
Method used
Image
Examples
Embodiment 1
[0037] A photothermal dual curing resin composition for pultrusion molding in this embodiment, said composition is composed of the following components by mass: 60 parts of bisphenol A epoxy acrylate, 25 parts of polypropylene glycol diacrylate, 5 parts of 2-hydroxy-2-methyl-1-phenylacetone, 2 parts of dibenzoyl peroxide, 1 part of KH-570, 1.5 parts of activated magnesium oxide, 0.5 parts of polydimethylsiloxane, p-hydroxybenzene 0.5 part of methyl ether, 0.5 part of zinc stearate.
[0038] The glass fiber composite material is prepared by using the above-mentioned photothermal dual curing resin composition for pultrusion molding, and the steps are as follows:
[0039] In parts by mass, 60 parts of bisphenol A epoxy acrylate, 25 parts of polypropylene glycol diacrylate, 1 part of KH-570, 1.5 parts of activated magnesium oxide, 0.5 parts of polydimethylsiloxane, and 0.5 parts of p-hydroxyanisole Add 0.5 parts of zinc stearate into a closed container, heat to 45°C and stir at h...
Embodiment 2
[0041]A photothermal dual curing resin composition for pultrusion molding in this embodiment, said composition is composed of the following components by mass: 65 parts of bisphenol A epoxy acrylate, 30 parts of tripropylene glycol diacrylate 6 parts of 1-hydroxycyclohexyl benzophenone, 3 parts of dibenzoyl peroxide, 1 part of KH-570, 2 parts of activated magnesium oxide, 0.6 parts of polydimethylsiloxane, 2,6-di-tert 0.6 parts of butyl p-cresol and 0.6 parts of zinc stearate.
[0042] The glass fiber composite material is prepared by using the above-mentioned photothermal dual curing resin composition for pultrusion molding, and the steps are as follows:
[0043] In parts by mass, 65 parts of bisphenol A epoxy acrylate, 30 parts of tripropylene glycol diacrylate, 1 part of KH-570, 2 parts of activated magnesium oxide, 0.6 parts of polydimethylsiloxane, 2,6- Add 0.6 parts of di-tert-butyl p-cresol and 0.6 parts of zinc stearate into a closed container, heat to 45°C and stir a...
Embodiment 3
[0045] A photothermal dual-curing resin composition for pultrusion molding in this embodiment, the composition is composed of the following components in parts by mass:
[0046] 65 parts of novolac epoxy acrylate, 30 parts of trimethylolpropane triacrylate, 6 parts of 2,4,6-trimethylbenzoyl-diphenylphosphine oxide, 3 parts of lauroyl peroxide, 1 part of KH -590, 2.5 parts of activated magnesium oxide, 0.6 parts of polydimethylsiloxane, 0.6 parts of 2,6-di-tert-butyl p-cresol, and 0.6 parts of zinc stearate.
[0047] The glass fiber composite material is prepared by using the above-mentioned photothermal dual curing resin composition for pultrusion molding, and the steps are as follows:
[0048] In parts by mass, 65 parts of novolac epoxy acrylate, 30 parts of trimethylolpropane triacrylate, 1 part of KH-590, 2.5 parts of activated magnesium oxide, 0.6 parts of polydimethylsiloxane, 2,6-dimethicone Add 0.6 parts of tert-butyl p-cresol and 0.6 parts of zinc stearate into a clos...
PUM
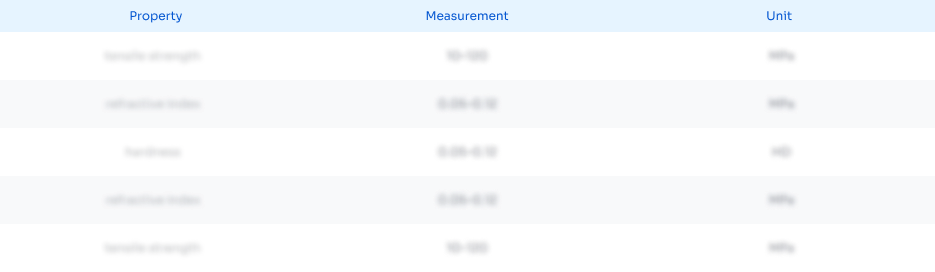
Abstract
Description
Claims
Application Information

- R&D Engineer
- R&D Manager
- IP Professional
- Industry Leading Data Capabilities
- Powerful AI technology
- Patent DNA Extraction
Browse by: Latest US Patents, China's latest patents, Technical Efficacy Thesaurus, Application Domain, Technology Topic, Popular Technical Reports.
© 2024 PatSnap. All rights reserved.Legal|Privacy policy|Modern Slavery Act Transparency Statement|Sitemap|About US| Contact US: help@patsnap.com