A high-temperature co-carbonization agent and its application in the carbonization process of plastic waste to increase carbon and fix impurities
A carbonization agent and waste technology, applied in other chemical processes, carbon compounds, reagents, etc., can solve the problems of reducing the content of impurity-containing small molecules, low solid carbonization rate, and low carbonization yield, so as to reduce the gas yield , Improve the yield of the carbonization process, and have a universal effect
- Summary
- Abstract
- Description
- Claims
- Application Information
AI Technical Summary
Problems solved by technology
Method used
Image
Examples
Embodiment 1
[0036]The polyurethane waste was desorbed to remove Freon residues, dried, and pulverized (200 mesh), and then coal tar pitch and polyurethane powder were mixed at a ratio of 0.3:1 to obtain carbonized raw materials (10 g). After putting into the carbonization chamber, nitrogen gas is introduced to remove the air in the carbonization chamber, and the whole reaction process is protected by nitrogen gas. When carbonizing, put the carbonized raw material into the high-temperature heating equipment at one time, the carbonized temperature is 300°C, the carbonized time is 8 hours, and the pressure is 5MPa. After the reaction is completed, the equipment is closed, and the solid product is taken out to obtain the carbonized material. The resulting carbonized material and activator CaCl 2 Mix according to the ratio of 2:1, add to the high-temperature heating equipment, pass the air in the nitrogen removal device, the activation temperature is 700°C, and the activation time is 1 hour. ...
Embodiment 2
[0038] The polyurethane waste was desorbed to remove Freon residues, dried and pulverized (200 mesh), and then coal tar pitch and polyurethane powder were mixed at a ratio of 0.3:1 to obtain carbonized raw materials (about 10 g). After putting into the carbonization chamber, nitrogen gas is introduced to remove the air in the carbonization chamber, and the whole reaction process is protected by nitrogen gas. When carbonizing, put the carbonized raw material into the high-temperature heating equipment at one time, the carbonized temperature is 400°C, the carbonized time is 8 hours, and the pressure is 5MPa. After the reaction is completed, the equipment is closed, and the solid product is taken out to obtain the carbonized material. The resulting carbonized material and activator CaCl 2 Mix according to the ratio of 2:1, add to the high-temperature heating equipment, pass the air in the nitrogen removal device, the activation temperature is 700°C, and the activation time is 1 h...
Embodiment 3
[0040] The polyurethane waste was desorbed to remove Freon residues, dried and pulverized (200 mesh), and then coal tar pitch and polyurethane powder were mixed at a ratio of 0.3:1 to obtain carbonized raw materials (about 10 g). After putting into the carbonization chamber, nitrogen gas is introduced to remove the air in the carbonization chamber, and the whole reaction process is protected by nitrogen gas. When carbonizing, put the carbonized raw material into the high-temperature heating equipment at one time, the carbonized temperature is 500°C, the carbonized time is 8 hours, and the pressure is 5MPa. After the reaction is completed, the equipment is closed, and the solid product is taken out to obtain the carbonized material. The resulting carbonized material and activator CaCl 2 Mix according to the ratio of 2:1, add to the high-temperature heating equipment, pass the air in the nitrogen removal device, the activation temperature is 700°C, and the activation time is 1 h...
PUM
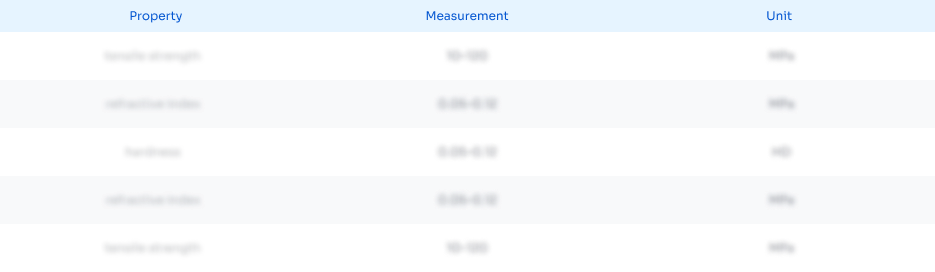
Abstract
Description
Claims
Application Information

- R&D
- Intellectual Property
- Life Sciences
- Materials
- Tech Scout
- Unparalleled Data Quality
- Higher Quality Content
- 60% Fewer Hallucinations
Browse by: Latest US Patents, China's latest patents, Technical Efficacy Thesaurus, Application Domain, Technology Topic, Popular Technical Reports.
© 2025 PatSnap. All rights reserved.Legal|Privacy policy|Modern Slavery Act Transparency Statement|Sitemap|About US| Contact US: help@patsnap.com