Branched type functionalized solution polymerized styrene-butadiene rubber and preparation method thereof
A solution-polymerized styrene-butadiene rubber and functionalization technology is applied in the field of solution-polymerized styrene-butadiene rubber containing siloxane branched modification and its synthesis, and can solve the problem that the comonomer is expensive and the functionalized solution-polymerized styrene-butadiene rubber is difficult to industrialize. and other problems, to achieve good wet skid resistance, excellent physical and mechanical properties, and improve product performance.
- Summary
- Abstract
- Description
- Claims
- Application Information
AI Technical Summary
Problems solved by technology
Method used
Image
Examples
Embodiment 1
[0030] In a jacketed 10L polymerization kettle, the system was replaced 3 times with nitrogen gas. Add 4088g of hexane, 160g of styrene, 480g of butadiene, and 0.51g of tetrahydrofuran to the polymerization kettle, raise the temperature to 40°C, add 4.3mmol of n-butyllithium, and naturally raise the temperature to 80-100°C. After 2 hours of polymerization, the conversion rate Reach 100%, the number average molecular weight of synthetic linear polymer is 150,000, and molecular weight distribution index is 1.2, adds 89mmol H-Si-(OC 8 h 17 )(C 12 h 25 ) 2 , 1.02mmol Speier catalyst (chloroplatinic acid hydrate) and 0.24mmol trichloroethylene, heated up to 100°C, continued to react for 1 hour, terminated the reaction, added anti-aging agent, discharged, the glue was coagulated by wet method, and dried. The nuclear magnetic test results show that the branched siloxane content accounts for 0.48wt% of the weight of the solution-polymerized styrene-butadiene rubber.
Embodiment 2
[0034] In a jacketed 10L polymerization kettle, the system was replaced 3 times with nitrogen gas. Add 5620g of cyclopentane, 220g of styrene, 660g of butadiene, and 0.38g of tetrahydrofurfuryl ether into the polymerization kettle, raise the temperature to 50°C, add 4.3mmol of n-butyllithium, naturally raise the temperature to 90-100°C, and polymerize for 1 hour Afterwards, conversion ratio reaches 100%, synthetic number average molecular weight is 200,000, and molecular weight distribution index is the linear polymkeric substance of 1.3, adds 85mmol H-Si-(OC 12 h 25 ) 3 , 0.15mmol Wilkinson catalyst (rhodium complex) and 0.11mmol ethylene glycol dimethyl ether, maintain the temperature at 90-100°C, continue the reaction for 1 hour, terminate the reaction, add anti-aging agent, discharge, the glue is coagulated by wet method ,drying. The nuclear magnetic test results show that the branched siloxane content accounts for 1.45% by weight of the solution-polymerized styrene-but...
Embodiment 3
[0038] In a jacketed 10L polymerization kettle, the system was replaced 3 times with nitrogen gas. Add 5620g of cyclohexane, 110g of styrene, 610g of butadiene, 0.51g of tetramethyldivinyldiamine into the polymerization kettle, raise the temperature to 50°C, add 2.9mmol of n-butyllithium, and naturally raise the temperature to 60-70°C , after 1.5 hours of polymerization, the conversion rate reached 100%, adding 0.87mmol tin tetrachloride coupling agent, the number average molecular weight obtained was 350,000, and the molecular weight distribution index was a star-shaped polymer of 1.4, adding 60mmol H-Si-(OC 10 h 21 ) 3 , 0.68mmol Wilkinson catalyst (rhodium complex) and 0.24mmol pyridine, maintain the temperature at 60-70°C, continue the reaction for 1.5 hours, terminate the reaction, add anti-aging agent, discharge, the glue is coagulated by wet method, and dried. The nuclear magnetic test results show that the siloxane branched chain content accounts for 2.42wt% of the w...
PUM
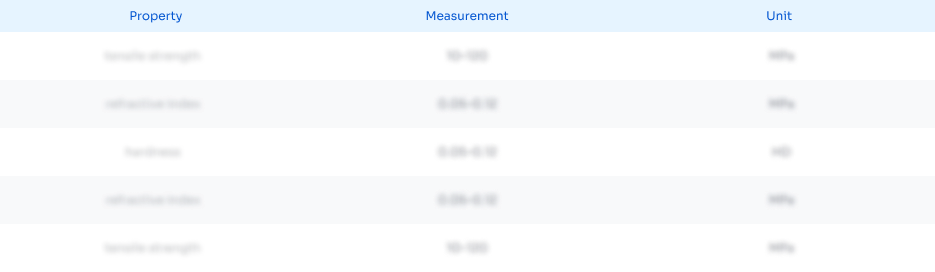
Abstract
Description
Claims
Application Information

- R&D
- Intellectual Property
- Life Sciences
- Materials
- Tech Scout
- Unparalleled Data Quality
- Higher Quality Content
- 60% Fewer Hallucinations
Browse by: Latest US Patents, China's latest patents, Technical Efficacy Thesaurus, Application Domain, Technology Topic, Popular Technical Reports.
© 2025 PatSnap. All rights reserved.Legal|Privacy policy|Modern Slavery Act Transparency Statement|Sitemap|About US| Contact US: help@patsnap.com