A kind of ultra-black wear-resistant coating and preparation method thereof
A manufacturing method and technology of wear-resistant coating, applied in the direction of coating, metal material coating process, vacuum evaporation plating, etc., can solve the problems of black color and wear-resistant performance that cannot meet high requirements, and achieve low cost , Hardness and wear resistance improvement, the effect of high wear resistance
- Summary
- Abstract
- Description
- Claims
- Application Information
AI Technical Summary
Problems solved by technology
Method used
Image
Examples
Embodiment 1
[0047] 1. The base material is ultrasonically cleaned, heated and vacuumed in the coating chamber, and the holding temperature is 200-230°C;
[0048] 2. The vacuum reaches 6.0*10-3~8.0*10-3Pa, and Ar gas is introduced to make the air pressure reach 0.1~0.2Pa, the bias voltage is -300~-400V, and ion cleaning is performed for 1~3 circles.
[0049] 3. Adjust the Ar gas intake to make the air pressure reach 0.3-0.4Pa, set the bias voltage to -50--100V, turn on the intermediate frequency coating power supply current to deposit pure Ti layer, and the titanium target current is 28-32A.
[0050] 4. Introduce N2 gas, the amount of N2 increases from 30sccm to 200sccm, the air pressure is 0.30~0.50Pa, and the Ti, Al, Si and W targets are turned on at the same time, and the target currents are respectively Ti=28~32A, Al=13~17A, Si =12~18A, W=3~7A, deposit WTiAlSiN layer for 30~40 minutes.
[0051] 5. Introduce N2 gas, the amount of N2 increases from 100sccm to 200sccm, the pressure is 0....
Embodiment 2
[0055] 1. The base material is ultrasonically cleaned, heated and evacuated in the coating chamber, and the heat preservation temperature is 210°C;
[0056] 2. The vacuum reaches 6.0*10-3~8.0*10-3Pa, and Ar gas is introduced to make the air pressure reach 0.1~0.2Pa, the bias voltage is -300~-400V, and ion cleaning is performed for 1~3 circles.
[0057] 3. Adjust the Ar gas intake to make the air pressure reach 0.3-0.4Pa, set the bias voltage to -50--100V, turn on the Ti target, and deposit a pure Ti layer.
[0058] 4. Infuse N2 gas, the pressure is 0.30-0.40Pa, open the Ti, Al, Si and W targets at the same time, and deposit the WTiAlSiN layer for 30 minutes.
[0059] 5. Infuse N2 gas, adjust the gas pressure to 0.4-0.5 Pa, open the Ti, Al, Si and W targets at the same time, and deposit the WTiAlSiN layer for 65 minutes.
[0060] 6. Turn off the TiAlSi target, turn off N2, fill in C2H2, the air pressure is 0.3pa, and turn on the W target at the same time, deposit the WC layer,...
Embodiment 3
[0062] 1. The base material is ultrasonically cleaned, heated and evacuated in the coating chamber, and the heat preservation temperature is 210°C;
[0063] 2. The vacuum reaches 6.0*10-3~8.0*10-3Pa, and Ar gas is introduced to make the air pressure reach 0.1~0.2Pa, the bias voltage is -300~-400V, and ion cleaning is performed for 1~3 circles.
[0064] 3. Adjust the Ar gas intake to make the air pressure reach 0.3-0.4Pa, set the bias voltage to -50--100V, turn on the Ti target, and deposit a pure Ti layer.
[0065] 4. Infuse N2 gas, adjust the air pressure to 0.30-0.40Pa, open the Ti, Al, Si and W targets at the same time, and deposit the WTiAlSiN layer for 35 minutes.
[0066] 5. Infuse N2 gas, adjust the gas pressure to 0.4-0.5 Pa, open the Ti, Al, Si and W targets at the same time, and deposit the WTiAlSiN layer for 70 minutes.
[0067] 6. Turn off the TiAlSi target, turn off N2, fill in C2H2, the air pressure is 0.4pa, turn on the W target at the same time, deposit the WC...
PUM
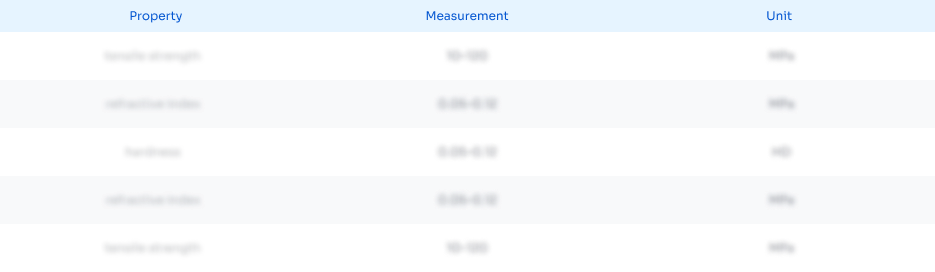
Abstract
Description
Claims
Application Information

- R&D
- Intellectual Property
- Life Sciences
- Materials
- Tech Scout
- Unparalleled Data Quality
- Higher Quality Content
- 60% Fewer Hallucinations
Browse by: Latest US Patents, China's latest patents, Technical Efficacy Thesaurus, Application Domain, Technology Topic, Popular Technical Reports.
© 2025 PatSnap. All rights reserved.Legal|Privacy policy|Modern Slavery Act Transparency Statement|Sitemap|About US| Contact US: help@patsnap.com