Process and system for continuous preparation of phenylenediamine
A preparation process, the technology of phenylenediamine, which is applied in the field of catalytic hydrogenation to synthesize aniline compounds, can solve the problems such as the danger of dinitrobenzene, and achieve low operating costs, less three wastes, and economically reasonable effects
- Summary
- Abstract
- Description
- Claims
- Application Information
AI Technical Summary
Problems solved by technology
Method used
Image
Examples
preparation example Construction
[0047] figure 1 It is a schematic diagram of the system composition of an embodiment of the preparation system of the present application, refer to below figure 1 The continuous preparation process and system of phenylenediamine of the present application will be described.
[0048] figure 1 Among them, the preparation system can be effectively applied to the continuous preparation process of, for example, phenylenediamine using benzene as a raw material, including a nitration unit, a washing unit, and a hydrogenation reduction unit connected in sequence through pipelines, and the nitration unit includes pipes connected in series Type reactor I1, phase separation device I7, tubular reactor II2 and phase separation device II8, the washing unit includes water washing tower I9, alkali washing tower 10 and water washing tower II20 connected in sequence, and the hydrogenation reduction unit includes The vertical pipe reactor III3, the first gas-liquid separator 11, the skeleton n...
Embodiment 1
[0053] A continuous preparation process of phenylenediamine, comprising the following steps:
[0054] 1) Nitric acid and sulfuric acid are mixed to form mixed acid I, and the mass percentage of said mixed acid I is composed of: 15% sulfuric acid, 75% nitric acid, and 10% water; benzene and mixed acid I are continuously fed into solids filled with 7g MCM-41 molecular sieves. React in the tubular reactor I of acid catalyst, the feed rate of benzene is 39 g / min, the feed rate of mixed acid is 44.1 g / min, the temperature of control tube reactor I is 35 ℃, and material is in tubular reaction After staying in the device Ⅰ for 1.3 hours, the material is discharged;
[0055] 2) The discharge obtained in step 1) is subjected to continuous phase separation to obtain acid phase I and organic phase I respectively, and the organic phase I and mixed acid II are continuously fed into a tubular reactor filled with 10 g of MCM-41 molecular sieve solid acid catalyst Ⅱ, the mass percentage of d...
Embodiment 2
[0065] A continuous preparation process of phenylenediamine, comprising the following steps:
[0066] 1) Mix nitric acid and sulfuric acid to form mixed acid I. The mass percentage of mixed acid I consists of: 20% sulfuric acid, 60% nitric acid, and 20% water; React in the tubular reactor I of acid catalyst, the feed rate of benzene is 46.8 g / min, the mixed acid I feed rate is 63 g / min, the temperature of control tube reactor I is 75 ℃, and the material is in the tubular reactor The material is discharged after staying in the reactor I for 0.2 hours;
[0067] 2) The discharge obtained in step 1) is continuously subjected to phase separation to obtain acid phase I and organic phase I respectively, and the organic phase I and mixed acid II are continuously sent into a tubular reactor filled with 10 g of HZSM-5 solid acid catalyst Ⅱ, the mass percentage of described mixed acid II is composed of: sulfuric acid 35%, nitric acid 60%, water 5%; The material is discharged after stay...
PUM
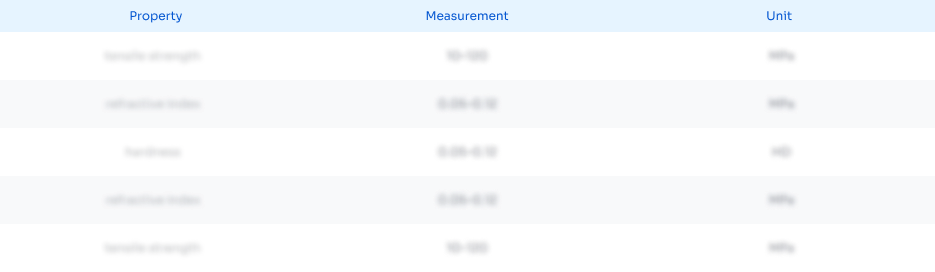
Abstract
Description
Claims
Application Information

- R&D
- Intellectual Property
- Life Sciences
- Materials
- Tech Scout
- Unparalleled Data Quality
- Higher Quality Content
- 60% Fewer Hallucinations
Browse by: Latest US Patents, China's latest patents, Technical Efficacy Thesaurus, Application Domain, Technology Topic, Popular Technical Reports.
© 2025 PatSnap. All rights reserved.Legal|Privacy policy|Modern Slavery Act Transparency Statement|Sitemap|About US| Contact US: help@patsnap.com