Cracking recovery process of n-butyl acrylate heavy components
A technology of n-butyl acrylate and heavy components, which is applied in the preparation of carboxylate esters, chemical industry, carboxylate preparation, etc. It can solve the problems of difficult separation by conventional means, reduce equipment maintenance rate and maintenance cost, and reduce energy consumption and material consumption, improve the effect of cracking rate and recovery rate
- Summary
- Abstract
- Description
- Claims
- Application Information
AI Technical Summary
Problems solved by technology
Method used
Image
Examples
Embodiment 1
[0036] The invention discloses a process for cracking and recovering the heavy component of n-butyl acrylate, which comprises the following steps: in the synthesis process of producing n-butyl acrylate with acrylic acid and n-butanol as raw materials, refining the n-butyl acrylate to the tower bottom component Put it into the bottom of the cracking kettle, add acrylic acid, catalyst, polymerization inhibitor, water in the cracking kettle at the same time, recover n-butyl acrylate from the top of the cracking kettle after cracking and discharge it into the recovery tower, the top of the recovery tower is mixed with n-butyl acrylate The reaction kettle is connected to realize the recombination and splitting of n-butyl acrylate, and then enters the esterification section to participate in the reaction and realize recovery; the cracking kettle includes a cracking section and a recovery section; the reaction conditions of the cracking section are: the operating temperature is 180°C, ...
Embodiment 2
[0044] The invention discloses a process for cracking and recovering the heavy component of n-butyl acrylate, which comprises the following steps: in the synthesis process of producing n-butyl acrylate with acrylic acid and n-butanol as raw materials, refining the n-butyl acrylate to the tower bottom component Put it into the bottom of the cracking kettle, add acrylic acid, catalyst, polymerization inhibitor, water in the cracking kettle at the same time, recover n-butyl acrylate from the top of the cracking kettle after cracking and discharge it into the recovery tower, the top of the recovery tower is mixed with n-butyl acrylate The reaction kettle is connected to realize the recombination and splitting of n-butyl acrylate, and then enters the esterification section to participate in the reaction and realize recovery; the cracking kettle includes a cracking section and a recovery section; the reaction conditions of the cracking section are: the operating temperature is 160°C, ...
Embodiment 3
[0052] The invention discloses a process for cracking and recovering the heavy component of n-butyl acrylate, which comprises the following steps: in the synthesis process of producing n-butyl acrylate with acrylic acid and n-butanol as raw materials, refining the n-butyl acrylate to the tower bottom component Put it into the bottom of the cracking kettle, add acrylic acid, catalyst, polymerization inhibitor, water in the cracking kettle at the same time, recover n-butyl acrylate from the top of the cracking kettle after cracking and discharge it into the recovery tower, the top of the recovery tower is mixed with n-butyl acrylate The reaction kettle is connected to realize the recombination and splitting of n-butyl acrylate, and then enters the esterification section to participate in the reaction and realize recovery; the cracking kettle includes a cracking section and a recovery section; the reaction conditions of the cracking section are: the operating temperature is 140°C, ...
PUM
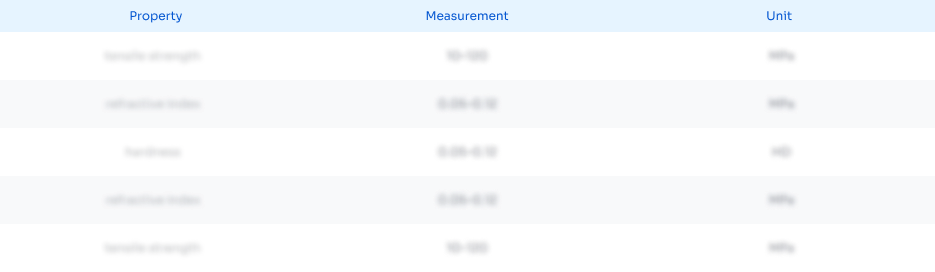
Abstract
Description
Claims
Application Information

- R&D
- Intellectual Property
- Life Sciences
- Materials
- Tech Scout
- Unparalleled Data Quality
- Higher Quality Content
- 60% Fewer Hallucinations
Browse by: Latest US Patents, China's latest patents, Technical Efficacy Thesaurus, Application Domain, Technology Topic, Popular Technical Reports.
© 2025 PatSnap. All rights reserved.Legal|Privacy policy|Modern Slavery Act Transparency Statement|Sitemap|About US| Contact US: help@patsnap.com