A method for high-strength soft tooling to realize co-curing of L-shaped ribs and C-shaped frame structure composite parts
A high-strength, ribbed technology, applied in the field of high-performance carbon fiber composite structural parts manufacturing, can solve the problems of reduced production efficiency, increased production cost, and increased manufacturing cycle, achieving high manufacturing success rate, short production cycle, and low manufacturing cost. low effect
- Summary
- Abstract
- Description
- Claims
- Application Information
AI Technical Summary
Problems solved by technology
Method used
Image
Examples
Embodiment 1
[0036] A method for high-strength soft tooling to realize co-curing of L-shaped ribs and C-shaped frame structure composite parts, comprising the following steps:
[0037] Step 1: Mold making, through the method of mechanical manufacturing, process two sets of metal forming molds that are exactly the same size as the left and right sides of the composite material parts, such as figure 1 with 2 The left metal mold and the right metal mold shown and as image 3 A set of C-shaped metal forming molds that are completely consistent with the inner surface of the C-shaped web of the workpiece are shown, and corresponding drilling templates are equipped at the ends of the three sets of metal molds for drilling after curing;
[0038] Step 2: Lay a layer of rubber on the left and right metal forming molds respectively. After the first layer of rubber is paved, continue to pave two layers of carbon fiber prepreg or glass fiber prepreg on the rubber layer as a reinforcement layer;
[00...
Embodiment 2
[0043] A method for high-strength soft tooling to realize co-curing of L-shaped ribs and C-shaped frame structure composite parts, comprising the following steps:
[0044] Step 1: Mold making, through the method of mechanical manufacturing, process two sets of metal forming molds that are exactly the same size as the left and right sides of the composite material parts, such as figure 1 with 2 The left metal mold and the right metal mold shown and as image 3 A set of C-shaped metal forming molds that are completely consistent with the inner surface of the C-shaped web of the workpiece are shown, and corresponding drilling templates are equipped at the ends of the three sets of metal molds for drilling after curing;
[0045] Step 2: Lay a layer of rubber on the left and right metal forming molds respectively. After the first layer of rubber is paved, continue to pave 10 layers of carbon fiber prepreg or glass fiber prepreg on the rubber layer as a reinforcement layer;
[0046]...
Embodiment 3
[0050] A method for high-strength soft tooling to realize co-curing of L-shaped ribs and C-shaped frame structure composite parts, comprising the following steps:
[0051] Step 1: Mold making, through the method of mechanical manufacturing, process two sets of metal forming molds that are exactly the same size as the left and right sides of the composite material parts, such as figure 1 with 2 The left metal mold and the right metal mold shown and as image 3 A set of C-shaped metal forming molds that are completely consistent with the inner surface of the C-shaped web of the workpiece are shown, and corresponding drilling templates are equipped at the ends of the three sets of metal molds for drilling after curing;
[0052] Step 2: Lay a layer of rubber on the left and right metal forming molds respectively. After the first layer of rubber is paved, continue to pave 5 layers of carbon fiber prepreg or glass fiber prepreg on the rubber layer as a reinforcement layer;
[0053...
PUM
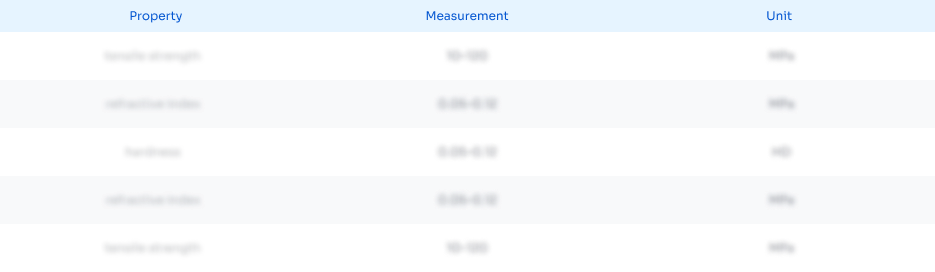
Abstract
Description
Claims
Application Information

- R&D Engineer
- R&D Manager
- IP Professional
- Industry Leading Data Capabilities
- Powerful AI technology
- Patent DNA Extraction
Browse by: Latest US Patents, China's latest patents, Technical Efficacy Thesaurus, Application Domain, Technology Topic, Popular Technical Reports.
© 2024 PatSnap. All rights reserved.Legal|Privacy policy|Modern Slavery Act Transparency Statement|Sitemap|About US| Contact US: help@patsnap.com