Manufacturing method for molding-type insulation connector of high-voltage cross-linked polyethylene insulated cable
A technology of cross-linked polyethylene and insulated cables, which is applied in the direction of cable installation, equipment for connecting/terminating cables, cable installation devices, etc. Uniform and stable thermal field distribution, reduced infrastructure costs, and long-lasting service life
- Summary
- Abstract
- Description
- Claims
- Application Information
AI Technical Summary
Problems solved by technology
Method used
Image
Examples
Embodiment 1
[0035] Making YJLW03-Z-64 / 110KV 1*800mm 2 The method of cross-linked polyethylene insulated cable molded insulation joints first builds a clean room and a work platform on site, and then proceeds in accordance with the standard operating instructions. The specific steps include:
[0036] 1) Cable stripping and pretreatment: Strip the cable end layer by layer according to the requirements of the drawing, insert the insulating copper shell in advance, and then perform pretreatment on the cable. The pretreatment includes but is not limited to the corrugated aluminum sheathing of the cable. The surface of the sheath is cleaned, the port of the corrugated aluminum sheath is turned into a trumpet shape and the burrs are removed, the corrugated aluminum sheath is coated with a layer of "bottom lead" with a transitional lead strip, the heating and straightening of the cable connection end, and the cable Insulation cutting and surface grinding of cable insulation.
[0037] 2) Conducto...
Embodiment 2
[0050] Make YJLW03-Z-127 / 220KV 1*800mm 2 The method of cross-linked polyethylene insulated cable molded insulation joints first builds a clean room and a work platform on site, and then proceeds in accordance with the standard operating instructions. The specific steps include:
[0051] 1) Cable stripping and pretreatment: Strip the cable end layer by layer according to the requirements of the drawing, insert the insulating copper shell in advance, and then perform pretreatment on the cable. The pretreatment includes but is not limited to the corrugated aluminum sheathing of the cable. The surface of the sheath is cleaned, the port of the corrugated aluminum sheath is turned into a trumpet shape and the burrs are removed, the corrugated aluminum sheath is coated with a layer of "bottom lead" with a transitional lead strip, the heating and straightening of the cable connection end, and the cable Insulation cutting and surface grinding of cable insulation.
[0052] 2) Conductor...
PUM
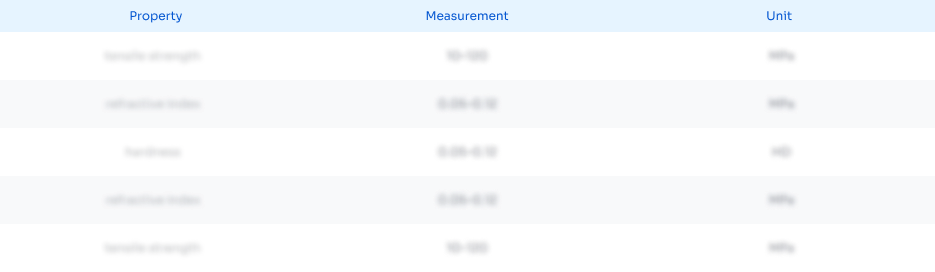
Abstract
Description
Claims
Application Information

- Generate Ideas
- Intellectual Property
- Life Sciences
- Materials
- Tech Scout
- Unparalleled Data Quality
- Higher Quality Content
- 60% Fewer Hallucinations
Browse by: Latest US Patents, China's latest patents, Technical Efficacy Thesaurus, Application Domain, Technology Topic, Popular Technical Reports.
© 2025 PatSnap. All rights reserved.Legal|Privacy policy|Modern Slavery Act Transparency Statement|Sitemap|About US| Contact US: help@patsnap.com