Uniaxial stretching device used with neutron scattering and experimental method
A neutron scattering and stretching device technology, which is applied in measuring devices, using wave/particle radiation for material analysis, and applying stable tension/pressure to test the strength of materials, etc. The material regulates the loading mode of the external field, cannot control the strain rate, and the temperature separately, etc., to achieve the effect of small installation size, convenient replacement, and avoiding the accumulation of errors
- Summary
- Abstract
- Description
- Claims
- Application Information
AI Technical Summary
Problems solved by technology
Method used
Image
Examples
Embodiment 1
[0030] The base is provided with a two-way lead screw 9, the two-way lead screw is connected with the mechanical deceleration mechanism 3, the mechanical deceleration mechanism is connected with the servo motor 1, and the motion controller 2 can be compiled to control the servo motor 1, and the two ends of the two-way lead screw 9 have opposite thread directions. The two-way screw 9 is provided with a two-way transmission mechanism 4, the two-way transmission mechanism 4 includes two sliding tables, and the two slides are respectively set on the two ends of the two-way screw 9, and the threaded holes on the slide table are respectively corresponding to the two-way screw 9. A heating chamber 7 is provided between the two sliding tables, and clamps are arranged at opposite ends of the heating chamber, the clamps are connected to the tension sensor 6, and the tension sensor 6 is connected to the sliding table.
[0031] The present invention uses process as follows:
[0032] Step ...
Embodiment 2
[0043] Preferably, a laser displacement sensor 8 is installed on the upper guide rail of the two-way transmission mechanism to provide independent position information, detect and correct the stretching process, avoid accumulating errors, and improve the reliability of the equipment.
[0044] Other structures of this embodiment are the same as Embodiment 1.
Embodiment 3
[0046] Preferably, there is an AI temperature controller in the heating chamber 7 to accurately control the temperature, and the temperature information detected by the thermal resistance is fed back to the AI temperature controller to automatically adjust the working state to achieve the purpose of precise temperature control, and nitrogen gas is introduced to ensure that the polymer film The sample is heated evenly.
[0047] Other structures of this embodiment are the same as Embodiment 1.
PUM
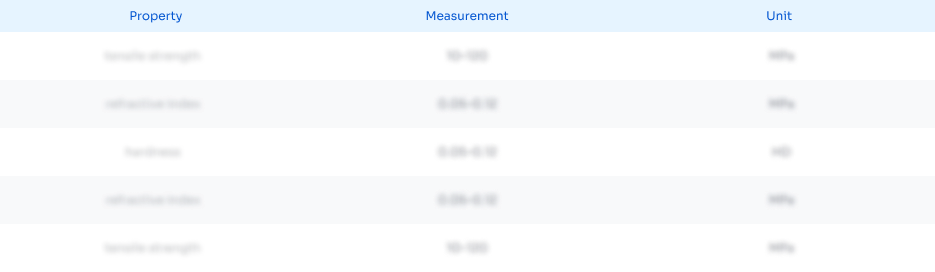
Abstract
Description
Claims
Application Information

- Generate Ideas
- Intellectual Property
- Life Sciences
- Materials
- Tech Scout
- Unparalleled Data Quality
- Higher Quality Content
- 60% Fewer Hallucinations
Browse by: Latest US Patents, China's latest patents, Technical Efficacy Thesaurus, Application Domain, Technology Topic, Popular Technical Reports.
© 2025 PatSnap. All rights reserved.Legal|Privacy policy|Modern Slavery Act Transparency Statement|Sitemap|About US| Contact US: help@patsnap.com