Preparation method of high-performance glass bottle
A glass bottle, high-performance technology, applied in glass manufacturing equipment, glass blowing, glass molding, etc., can solve the problems of uneven quality, poor performance, and low strength of glass bottles, and achieve increased chemical stability and improved Transparency, the effect of removing internal stress
- Summary
- Abstract
- Description
- Claims
- Application Information
AI Technical Summary
Problems solved by technology
Method used
Examples
Embodiment 1
[0032] 100 parts of quartz sand, 75 parts of cullet, 30 parts of limestone, 20 parts of dolomite, 10 parts of cobalt oxide, 15 parts of nickel oxide, 12 parts of sodium nitrate, 5 parts of manganese dioxide, 30 parts of borax, 12 parts of zinc oxide, 5 parts of Glauber's salt, 6 parts of barium sulfate, 25 parts of potassium carbonate, 25 parts of barium sulfate and 40 parts of boric acid are used as raw materials, and the raw materials prepared above are crushed and ground in batches using a ball mill. The grinding time is 6 hours, and the grinding ball-to-material ratio is 7:1, the grinding speed is 260r / min;
[0033] Dry the crushed raw materials to reduce the moisture content. The drying temperature is 100°C and the drying time is 3 hours. During the drying process, the raw materials need to be stirred continuously. If the raw materials contain metal impurities, it is necessary to Carry out iron removal treatment on the raw materials, and then add all the raw materials to ...
Embodiment 2
[0039] 140 parts of quartz sand, 105 parts of cullet, 35 parts of limestone, 25 parts of dolomite, 12 parts of cobalt oxide, 17 parts of nickel oxide, 14 parts of sodium nitrate, 7 parts of manganese dioxide, 35 parts of borax, 14 parts of zinc oxide, 6 parts of Glauber's salt, 7 parts of barium sulfate, 27 parts of potassium carbonate, 27 parts of barium sulfate and 42 parts of boric acid are used as raw materials, and the raw materials prepared above are crushed and ground in batches using a ball mill. The grinding time is 5 hours, and the grinding ball-to-material ratio is 7:1, the grinding speed is 260r / min;
[0040] Dry the pulverized raw materials to reduce the moisture content. The drying temperature is 120°C and the drying time is 3 hours. During the drying process, the raw materials need to be stirred continuously. Carry out iron removal treatment on the raw materials, and then add all the raw materials to the mixing device for stirring and mixing, so that the raw mat...
Embodiment 3
[0046] 150 parts of quartz sand, 110 parts of cullet, 37 parts of limestone, 26 parts of dolomite, 12.5 parts of cobalt oxide, 17.5 parts of nickel oxide, 14.5 parts of sodium nitrate, 8 parts of manganese dioxide, 37 parts of borax, 15 parts of zinc oxide, 6.5 parts of Glauber's salt, 7.5 parts of barium sulfate, 27.5 parts of potassium carbonate, 27.5 parts of barium sulfate and 42.5 parts of boric acid are used as raw materials, and the raw materials prepared above are crushed and ground in batches using a ball mill. The grinding time is 8 hours, and the grinding ball-to-material ratio is 8:1, the grinding speed is 255r / min;
[0047] Dry the pulverized raw materials to reduce the moisture content. The drying temperature is 110°C and the drying time is 2.5 hours. During the drying process, the raw materials need to be stirred continuously. If the raw materials contain metal impurities, the It is necessary to remove iron from the raw materials, and then add all the raw materi...
PUM
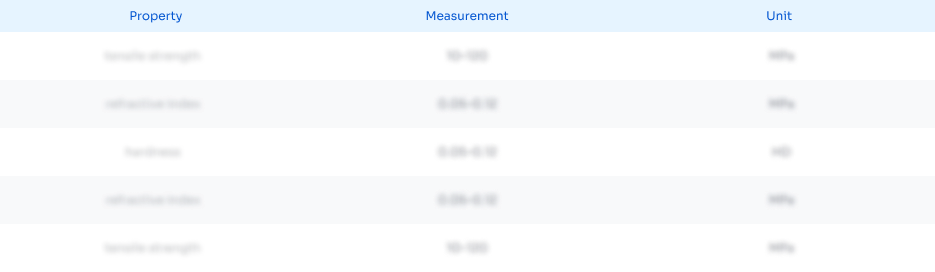
Abstract
Description
Claims
Application Information

- R&D
- Intellectual Property
- Life Sciences
- Materials
- Tech Scout
- Unparalleled Data Quality
- Higher Quality Content
- 60% Fewer Hallucinations
Browse by: Latest US Patents, China's latest patents, Technical Efficacy Thesaurus, Application Domain, Technology Topic, Popular Technical Reports.
© 2025 PatSnap. All rights reserved.Legal|Privacy policy|Modern Slavery Act Transparency Statement|Sitemap|About US| Contact US: help@patsnap.com