A processing technology of cast iron-nickel alloy spraying mold
A mold processing and nickel alloy technology, applied in the direction of manufacturing tools, furnaces, heat treatment equipment, etc., can solve the problems of mold quality influence, inability to heat the bottom of the mold, uneven heating, etc., achieve good quenching effect and reduce heating and quenching time Effect
- Summary
- Abstract
- Description
- Claims
- Application Information
AI Technical Summary
Problems solved by technology
Method used
Image
Examples
Embodiment Construction
[0033] The following will clearly and completely describe the technical solutions in the embodiments of the present invention with reference to the accompanying drawings in the embodiments of the present invention. Obviously, the described embodiments are only some, not all, embodiments of the present invention. Based on the embodiments of the present invention, all other embodiments obtained by persons of ordinary skill in the art without creative efforts fall within the protection scope of the present invention.
[0034] Such as Figure 1-3 As shown, a cast iron-nickel alloy spraying mold processing technology, including mold raw material blanking - forging forming - tempering - rough grinding - mold surface spray welding - mold quenching - mold annealing - mold quenching and tempering - fine grinding and polishing - mold Detection process steps, the specific steps are as follows;
[0035] (1) Mold raw material blanking: first determine the size of the mold to be processed,...
PUM
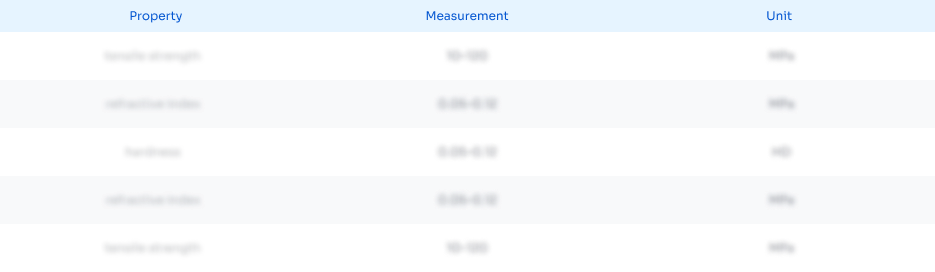
Abstract
Description
Claims
Application Information

- R&D Engineer
- R&D Manager
- IP Professional
- Industry Leading Data Capabilities
- Powerful AI technology
- Patent DNA Extraction
Browse by: Latest US Patents, China's latest patents, Technical Efficacy Thesaurus, Application Domain, Technology Topic, Popular Technical Reports.
© 2024 PatSnap. All rights reserved.Legal|Privacy policy|Modern Slavery Act Transparency Statement|Sitemap|About US| Contact US: help@patsnap.com