High-efficiency heat preservation foam plastic
A foam plastic and high-efficiency technology, which is applied in the field of foam plastic preparation, can solve problems such as poor thermal insulation performance, and achieve the effect of providing thermal insulation, improving thermal insulation, and absorbing light energy
- Summary
- Abstract
- Description
- Claims
- Application Information
AI Technical Summary
Problems solved by technology
Method used
Examples
preparation example Construction
[0034] The preparation method of composite thermal insulation base material comprises the following steps:
[0035](1) According to the mass ratio of 1:3~6:1:0.5~0.8, take titanium nickel yellow, rock wool, vitrified microbeads, and an ethanol solution with a volume fraction of 30% and mix them in a ball mill tank. Add zirconia ball milling beads at 30:1 and mix, mill at 350~550r / min for 1~3h to get ball mill, take the ball mill and add reagent A to mix and stir at a mass ratio of 1:12~20, stand at room temperature for 3~6h, filter , take the filter residue and wash it with mixed washing solution for 2~4 times, then move it to the muffle furnace for heat treatment at 600~800°C for 4~6h, and obtain the heat treatment material for later use;
[0036] (2) In a water bath at 25~30°C, mix a formaldehyde solution with a mass fraction of 37% and a NaOH solution with a concentration of 0.1mol / L in a container at a mass ratio of 10~15:1, and stir magnetically at 350~550r / min for 35~ 6...
Embodiment 1
[0044] Reagent A: Mix calcium bicarbonate and 20% sodium carbonate solution at a mass ratio of 1:4 to obtain reagent A.
[0045] Reagent B: Mix 20% citric acid solution and acrylamide at a mass ratio of 5:1 to obtain Reagent B.
[0046] Mixed lotion: According to the mass ratio of 4:1, take 70% ethanol solution and acetone and mix them to get the mixed lotion.
[0047] Modified material: Mix melamine, polyethylene glycol and mannitol according to the mass ratio of 5:1:0.1 to obtain the modified material.
[0048] Excipients: Mix simethicone, microcrystalline paraffin, and magnesium stearate at a mass ratio of 5:1:0.2 to obtain the excipients.
[0049] Plasticizer: Mix triethyl citrate and dioctyl phthalate at a mass ratio of 3:1 to obtain a plasticizer.
[0050] Foaming agent: Mix sodium lauryl sulfate and rosin soap at a mass ratio of 5:1 to obtain a foaming agent.
[0051] The preparation method of composite thermal insulation base material comprises the following steps: ...
Embodiment 2
[0061] Reagent A: Mix calcium bicarbonate and 20% sodium carbonate solution at a mass ratio of 1:6 to obtain reagent A.
[0062] Reagent B: Mix 20% citric acid solution and acrylamide at a mass ratio of 6:1 to obtain Reagent B.
[0063] Mixed lotion: Mix 70% ethanol solution and acetone at a mass ratio of 6:1 to obtain a mixed lotion.
[0064] Modified material: Mix melamine, polyethylene glycol and mannitol according to the mass ratio of 5:2:0.1 to obtain the modified material.
[0065] Excipients: Mix simethicone, microcrystalline paraffin, and magnesium stearate at a mass ratio of 5:2:0.3 to obtain the excipients.
[0066] Plasticizer: Mix triethyl citrate and dioctyl phthalate at a mass ratio of 4:1 to obtain a plasticizer.
[0067] Foaming agent: Mix sodium lauryl sulfate and rosin soap at a mass ratio of 5:2 to obtain a foaming agent.
[0068] The preparation method of composite thermal insulation base material comprises the following steps:
[0069] (1) According to...
PUM
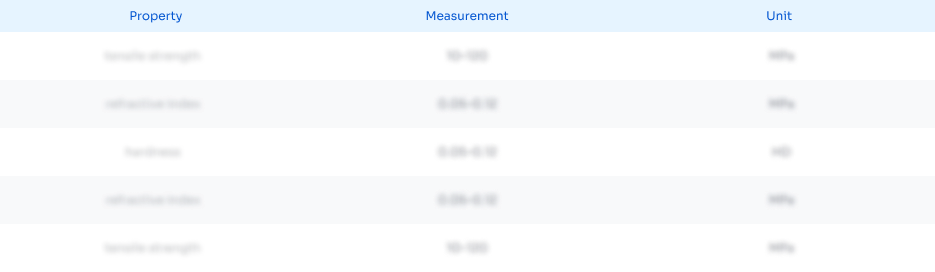
Abstract
Description
Claims
Application Information

- R&D Engineer
- R&D Manager
- IP Professional
- Industry Leading Data Capabilities
- Powerful AI technology
- Patent DNA Extraction
Browse by: Latest US Patents, China's latest patents, Technical Efficacy Thesaurus, Application Domain, Technology Topic, Popular Technical Reports.
© 2024 PatSnap. All rights reserved.Legal|Privacy policy|Modern Slavery Act Transparency Statement|Sitemap|About US| Contact US: help@patsnap.com