Planar receiving type centrifugal-spinning automatic production equipment and method
A technology of automatic production and centrifugal spinning, used in textiles and papermaking, fiber processing, non-woven fabrics, etc., can solve the problems of inability to achieve continuous production, low efficiency, and low safety factor.
- Summary
- Abstract
- Description
- Claims
- Application Information
AI Technical Summary
Problems solved by technology
Method used
Image
Examples
Embodiment 1
[0098] Such as figure 1 Shown, a kind of planar receiving type centrifugal spinning automatic production equipment comprises centrifugal spinning device 1, compacting device 2 and winding device 3; Described centrifugal spinning device 1, compacting device 2 and winding device 3 are according to centrifugal spinning fiber The direction of movement of the web 5 is arranged sequentially from front to back; the centrifugal spinning device 1 spins a centrifugal spinning fiber web 5; the centrifugal spinning fiber web 5 is introduced into the winding device 3 after being compacted by the compacting device 2 ; The winding device 3 winds the centrifugally spun web 5 into rolls.
[0099] Such as figure 2 As shown, the centrifugal spinning device 1 includes a frame 11, a feeding device 12, a spinning device 13, a collecting device 14, a temperature control device 15 and a control system 16; the feeding device 12 is fixedly installed at the bottom of the frame 11 The temperature cont...
Embodiment 2
[0143] The difference with embodiment 1 is that a kind of planar receiving type centrifugal spinning equipment in embodiment 2, such as Figure 12 As shown, it also includes an unwinding device 4, which is arranged at the front end of the centrifugal spinning device 1; the unwinding device 4 is wound with a base cloth 6; the base cloth 6 penetrates into the centrifugal spinning device 1; Spinning device 1, and flat on the collection belt 142; the end of the base fabric 6 is wound on the winding roller 319 on the winding device 3.
[0144] Such as Figure 13 As shown, the unwinding device 4 includes an unwinding roller 401, an unwinding frame 402, a clamping mechanism 317, a first guide roller 303, a third guide roller 403, a second guide roller 301 and a deviation correction device 322; The moving direction of the base cloth 6, the second guide roller 301, the third guide roller 403 and the first guide roller 303 are arranged in sequence, and are fixedly installed on the unwi...
Embodiment 3
[0148] The difference with embodiment 1 is that, in the spinner device 133 in embodiment 3, at least one spinneret 1354 is installed on its said spinneret 1340; The shape of shown spinneret is as follows Figure 14 As shown, its inner diameter gradually becomes smaller to form a cone; the spinning solution in the spinneret 1340 is ejected through the spinneret 1354 .
PUM
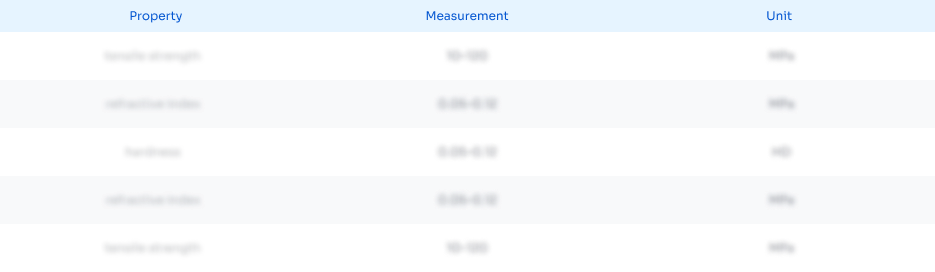
Abstract
Description
Claims
Application Information

- R&D
- Intellectual Property
- Life Sciences
- Materials
- Tech Scout
- Unparalleled Data Quality
- Higher Quality Content
- 60% Fewer Hallucinations
Browse by: Latest US Patents, China's latest patents, Technical Efficacy Thesaurus, Application Domain, Technology Topic, Popular Technical Reports.
© 2025 PatSnap. All rights reserved.Legal|Privacy policy|Modern Slavery Act Transparency Statement|Sitemap|About US| Contact US: help@patsnap.com