Low-temperature flue gas cooling system of shutdown combustor and parameter design method thereof
A low-temperature flue gas and cooling system technology, applied in the direction of combustion methods, combustion equipment, computer-aided design, etc., can solve the problems of aggravating ash and combustibles, increasing cooling air volume, and increasing power consumption of fans
- Summary
- Abstract
- Description
- Claims
- Application Information
AI Technical Summary
Problems solved by technology
Method used
Image
Examples
Embodiment 1
[0075] In this embodiment, a low-temperature flue gas cooling system for idle burners provided by the present invention is used to cool the primary tuyeres and secondary tuyeres of the idle burners of opposed combustion boilers, such as figure 1 As shown, the cooling system includes A, B boiler induced draft fan 1, main pipe 2, branch main pipe 4, branch pipe 5 and branch pipe 6;
[0076] The low-temperature flue gas is led out from the outlet flue openings of the induced draft fans of boilers A and B respectively. The nominal diameter of the openings is the inner diameter of the main pipe 2. Two parallel main pipes are welded and then merged into one main pipe 2. The inner diameter of each main pipe 2 is The same pipeline; the two parallel main pipes are equipped with main pipe electric isolation doors 3 for system isolation. A and B boiler induced draft fans 1 supply air at the same time to avoid the failure of a single boiler induced draft fan and cause the system to fail t...
Embodiment 2
[0082] In this embodiment, a low-temperature flue gas cooling system for idle burners provided by the present invention is used to cool the primary tuyeres and secondary tuyeres of the idle burners of tangential combustion boilers, such as figure 2 As shown, the cooling system includes A, B boiler induced draft fan 1, main pipe 2, branch main pipe 4, branch pipe 5 and branch pipe 6;
[0083] The low-temperature flue gas is led out from the outlet flue openings of the induced draft fans of boilers A and B respectively. The nominal diameter of the openings is the inner diameter of the main pipe 2. Two parallel main pipes 2 are welded and then merged into one main pipe 2. Each main pipe 2 is Pipelines with the same inner diameter; the two parallel main pipes 2 are equipped with main pipe electric isolation doors 3 for system isolation. A and B boiler induced draft fans 1 supply air simultaneously to avoid the failure of a single boiler induced draft fan and cause the system to f...
Embodiment 3
[0089] In this embodiment, a low-temperature flue gas cooling system for a burner that is out of service in Embodiment 1 or Embodiment 2 is adopted, and its parameter design method includes the following specific steps:
[0090] 1) Calculate the amount of cooling flue gas in the main pipe, branch main pipe, branch pipe and branch pipe according to the following steps:
[0091] 1.1) Calculate the amount of cooling flue gas in each cooling channel according to the following formula:
[0092]
[0093] Among them: Q i zgy Calculate the cooling flue gas volume for the i-th cooling channel, kg / h, i∈[1,N]; N is the total number of cooling channels in the idle burner, (the cooling flue gas volume of the i-th cooling channel is the i-th connected to it Cooling flue gas volume in the branch pipe), where,
[0094] For opposed combustion boilers, the maximum number of cooling channels for each primary air swirl burner is 4, and the maximum number of cooling channels for each ember b...
PUM
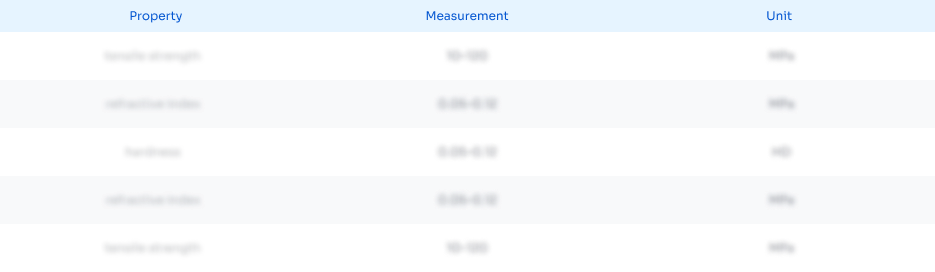
Abstract
Description
Claims
Application Information

- R&D
- Intellectual Property
- Life Sciences
- Materials
- Tech Scout
- Unparalleled Data Quality
- Higher Quality Content
- 60% Fewer Hallucinations
Browse by: Latest US Patents, China's latest patents, Technical Efficacy Thesaurus, Application Domain, Technology Topic, Popular Technical Reports.
© 2025 PatSnap. All rights reserved.Legal|Privacy policy|Modern Slavery Act Transparency Statement|Sitemap|About US| Contact US: help@patsnap.com