A crystallizer for continuous casting equipment
A mold and equipment technology, applied in the field of steel processing, can solve the problems of increasing the resistance of molten steel, unstable eddy current, uneven heat conduction of the mold, and achieve the effects of reducing the contact time, increasing the stability, and reducing the resistance.
- Summary
- Abstract
- Description
- Claims
- Application Information
AI Technical Summary
Problems solved by technology
Method used
Image
Examples
Embodiment Construction
[0018] The following will clearly and completely describe the technical solutions in the embodiments of the present invention with reference to the accompanying drawings in the embodiments of the present invention. Obviously, the described embodiments are only some, not all, embodiments of the present invention. Based on the embodiments of the present invention, all other embodiments obtained by persons of ordinary skill in the art without making creative efforts belong to the protection scope of the present invention.
[0019] see Figure 1-3 , a crystallizer for continuous casting equipment, comprising a steel shell 1, a water distribution plate 2, a water inlet pipe 3, and a water outlet pipe 4, the water distribution plate 2 is installed on the outer wall of the steel structure shell 1, and the water inlet pipe 3 is installed on the water distribution plate 2, the water outlet pipe 4 is arranged at the bottom of the steel structure shell 1, and a cover plate 5 is installed...
PUM
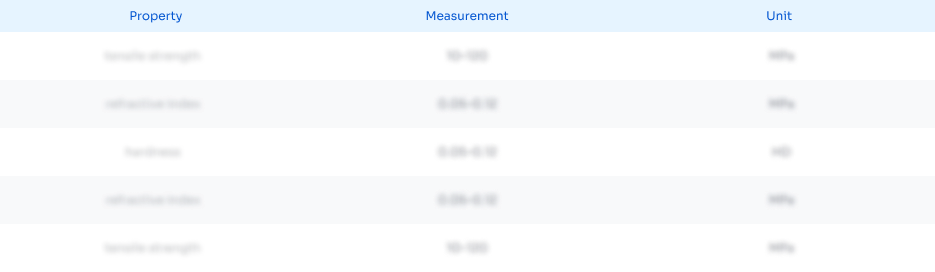
Abstract
Description
Claims
Application Information

- Generate Ideas
- Intellectual Property
- Life Sciences
- Materials
- Tech Scout
- Unparalleled Data Quality
- Higher Quality Content
- 60% Fewer Hallucinations
Browse by: Latest US Patents, China's latest patents, Technical Efficacy Thesaurus, Application Domain, Technology Topic, Popular Technical Reports.
© 2025 PatSnap. All rights reserved.Legal|Privacy policy|Modern Slavery Act Transparency Statement|Sitemap|About US| Contact US: help@patsnap.com