Method for improving manufacturing precision of components at head switching section of annular flame cylinder
A flame tube head and manufacturing precision technology, which is applied in the field of improving the manufacturing accuracy of the ring-shaped flame tube head adapter section assembly, can solve the problem of large deformation of the head adapter section, small deformation control effect, large welding stress and welding deformation, etc. problems, to achieve the effect of improving manufacturing precision, realizing precise forming and high production efficiency
- Summary
- Abstract
- Description
- Claims
- Application Information
AI Technical Summary
Problems solved by technology
Method used
Image
Examples
Embodiment Construction
[0040] The present invention is described in further detail below in conjunction with accompanying drawing:
[0041] A method for improving the manufacturing accuracy of an annular flame cylinder head adapter section assembly, comprising the following steps:
[0042] 1) Pre-forming the head transition section: using sheet metal for stamping pre-forming to form the preliminary head transition section, which has a constant cross-sectional shape structure, such as image 3 a. image 3 As shown in b, there is no convex structure on the surface of the constant cross-sectional shape structure; the profile thickness of the preliminary head transition section is greater than the minimum wall thickness of the profile of the head transition section after molding;
[0043] Specifically, sheet metal stamping is used to form the preliminary head transfer section, and then the preliminary head transfer section is punched out to pre-puncher the vortex device installation hole, and the vorte...
PUM
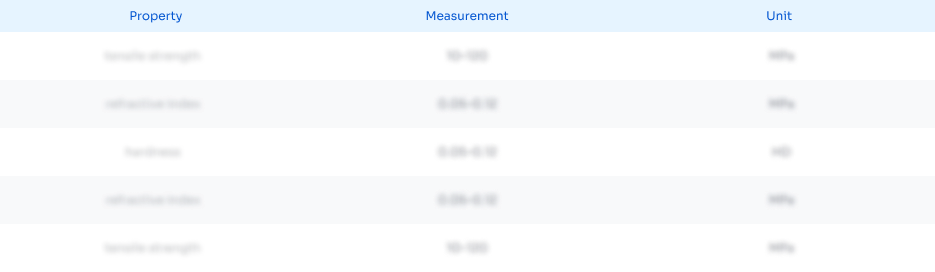
Abstract
Description
Claims
Application Information

- R&D
- Intellectual Property
- Life Sciences
- Materials
- Tech Scout
- Unparalleled Data Quality
- Higher Quality Content
- 60% Fewer Hallucinations
Browse by: Latest US Patents, China's latest patents, Technical Efficacy Thesaurus, Application Domain, Technology Topic, Popular Technical Reports.
© 2025 PatSnap. All rights reserved.Legal|Privacy policy|Modern Slavery Act Transparency Statement|Sitemap|About US| Contact US: help@patsnap.com