Design methods of synchronous motors
A design method and motor technology, applied in the control of generators, motor-generator control, electronic commutation motor control, etc., can solve the problems of slow convergence of two-dimensional electromagnetic field finite element analysis method, long calculation time, inability to meet rapid design and other problems
- Summary
- Abstract
- Description
- Claims
- Application Information
AI Technical Summary
Problems solved by technology
Method used
Image
Examples
Embodiment 1
[0194]Design a 22kW, 1500r / min three-phase permanent magnet synchronous motor with a rated voltage of 380V, a frame size of 160, a stator outer diameter of 260mm, a stator inner diameter of 180mm, a stack length of 200mm, an air gap of 0.7mm, and a rotor inner diameter of 60mm. Built-in V-shaped structure, the magnetic steel adopts N38UH NdFeB permanent magnet material, the stator and rotor core material is 35WW300 silicon steel sheet, the stator winding star connection, double-layer stacked winding, the number of conductors per slot is 30, parallel branch 4, the wire is Three 0.8mm enamelled round copper wires are wound together. The section of the stator and rotor punching and winding of the three-phase permanent magnet synchronous motor is as follows: figure 1 As shown, the design process is as follows figure 2 shown.
[0195] step 1,
[0196] The 2D electromagnetic field transient motion model of the motor is established in Ansoft Maxwell 2D. The parameters of the main...
Embodiment 2
[0351] Embodiment 2 adopts the same electromagnetic parameters of the three-phase permanent magnet synchronous motor as the embodiment, and the output power and voltage are also the same. Design flow chart such as figure 2 shown.
[0352] step 1,
[0353] Establish the 2D electromagnetic field transient motion model of the motor to be designed in Ansoft Maxwell 2D. The parameters of the main materials and dimensions are the same as those based on the magnetic circuit analysis method. The current source is used for excitation and set to zero current, especially in the material setting Check the core material loss characteristic parameters and select the stator core part in the Excitations>Set Core Loss menu. Calculate a period (10ms) of the electromagnetic field that rotates at a certain speed, and the step size is 1 / 100 of the period, that is, 0.1ms. Obtain the excitation electromotive force curve on any phase coil of the period through the post-processing software, and pe...
Embodiment 3
[0511] Design a 7.5kW, 1500r / min three-phase synchronous reluctance motor, rated at 380V, using a frame size of 160, with a stator outer diameter of 260mm, a stator inner diameter of 180mm, a stack length of 200mm, an air gap of 0.7mm, and a rotor inner diameter of 60mm. Multi-layer magnetic barrier structure, stator and rotor core material is 35WW300 silicon steel sheet, stator winding star connection, double-layer stacked winding, 40 conductors per slot, 4 parallel branches, and two 0.85mm enamelled round copper wires are wound together. Stator and rotor punching and winding section of three-phase synchronous reluctance motor Figure 9 shown. Design flow chart such as Figure 11 shown.
[0512] step 1,
[0513] Set direct axis synchronous reactance conversion coefficient k xd , Quadrature axis synchronous reactance conversion coefficient k xq , the ratio of load iron loss to output power k pfe2 The initial value; generally set the initial value: k xd =0.2,k xq =0.8,k...
PUM
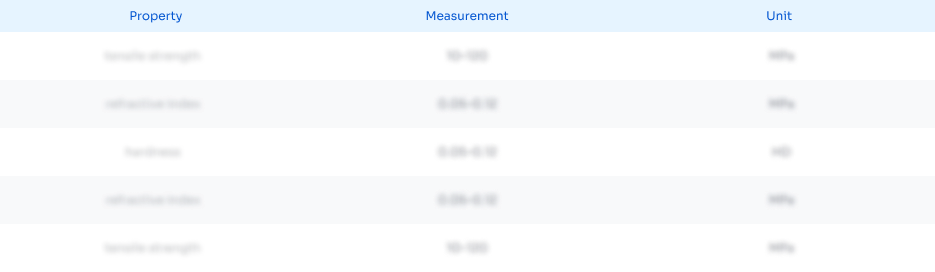
Abstract
Description
Claims
Application Information

- R&D
- Intellectual Property
- Life Sciences
- Materials
- Tech Scout
- Unparalleled Data Quality
- Higher Quality Content
- 60% Fewer Hallucinations
Browse by: Latest US Patents, China's latest patents, Technical Efficacy Thesaurus, Application Domain, Technology Topic, Popular Technical Reports.
© 2025 PatSnap. All rights reserved.Legal|Privacy policy|Modern Slavery Act Transparency Statement|Sitemap|About US| Contact US: help@patsnap.com