Preparation method of cuprous oxide antibacterial textile
A technology of antibacterial textiles and cuprous oxide, which is applied in textiles and papermaking, biochemical fiber treatment, ultrasonic/sonic fiber treatment, etc., can solve the problems of antibacterial textiles that are not resistant to water washing, poor combination fastness between cuprous oxide and textiles, and achieve Effect of improving bonding fastness and increasing load capacity
- Summary
- Abstract
- Description
- Claims
- Application Information
AI Technical Summary
Problems solved by technology
Method used
Image
Examples
Embodiment 1
[0021] (1) Place the cellulose fiber fabric on the shelf in the chamber of the DT-01 low-temperature plasma processing apparatus produced by Suzhou Opus Plasma Technology Co., Ltd., turn on the vacuum pump, and when the vacuum degree in the reaction chamber is 5Pa, feed Nitrogen gas into the plasma chamber, adjust the gas flow until the vacuum degree in the reaction chamber is 20Pa; after 3 minutes of stabilization, glow discharge, discharge power 50W, discharge time 15min, after the discharge, take out the fabric and immediately enter the next step;
[0022] (2) Dissolve commercially available silk peptide powder with a molecular weight of 500-5000 in deionized water to prepare a silk peptide solution with a mass fraction of 1%; then immerse the cellulose fiber fabric treated in step (1) into the silk peptide solution , treated at 30°C for 60 minutes, after the treatment, dried at 80°C, then baked at 130°C for 5 minutes, finally washed with deionized water for 3 times, dried a...
Embodiment 2
[0040] (1) Place the cellulose fiber fabric on the shelf in the chamber of the DT-01 low-temperature plasma processing apparatus produced by Suzhou Opus Plasma Technology Co., Ltd., turn on the vacuum pump, and when the vacuum degree in the reaction chamber is 5Pa, feed Nitrogen gas is injected into the plasma chamber, and the gas flow rate is adjusted until the vacuum degree in the reaction chamber is 50 Pa; after 3 minutes of stabilization, glow discharge is performed, the discharge power is 150W, and the discharge time is 5 minutes. After the discharge is completed, take out the fabric and immediately enter the next step;
[0041] (2) Dissolve commercially available silk peptide powder with a molecular weight of 500-5000 in deionized water to prepare a silk peptide solution with a mass fraction of 10%; then immerse the cellulose fiber fabric treated in step (1) into the silk peptide solution In the process, treat at 50°C for 30 minutes, after the treatment, dry at 85°C, then...
Embodiment 3
[0044] (1) Place the cellulose fiber fabric on the shelf in the chamber of the DT-01 low-temperature plasma processing apparatus produced by Suzhou Opus Plasma Technology Co., Ltd., turn on the vacuum pump, and when the vacuum degree in the reaction chamber is 5Pa, feed Nitrogen is injected into the plasma chamber, and the gas flow rate is adjusted until the vacuum degree in the reaction chamber is 40 Pa; after 4 minutes of stabilization, glow discharge is performed, the discharge power is 100W, and the discharge time is 10 minutes. After the discharge is completed, the fabric is taken out and immediately enters the next step;
[0045] (2) Dissolve commercially available silk peptide powder with a molecular weight of 500-5000 in deionized water to prepare a silk peptide solution with a mass fraction of 5%; then immerse the cellulose fiber fabric treated in step (1) into the silk peptide solution In the process, treat at 40°C for 40 minutes. After the treatment, dry at 82°C, the...
PUM
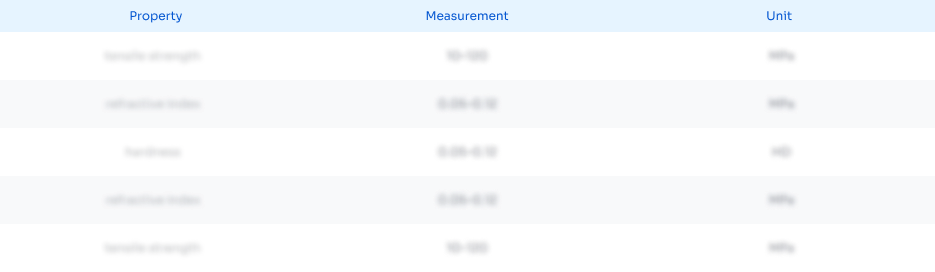
Abstract
Description
Claims
Application Information

- Generate Ideas
- Intellectual Property
- Life Sciences
- Materials
- Tech Scout
- Unparalleled Data Quality
- Higher Quality Content
- 60% Fewer Hallucinations
Browse by: Latest US Patents, China's latest patents, Technical Efficacy Thesaurus, Application Domain, Technology Topic, Popular Technical Reports.
© 2025 PatSnap. All rights reserved.Legal|Privacy policy|Modern Slavery Act Transparency Statement|Sitemap|About US| Contact US: help@patsnap.com