Air gap magnetic core burr removing mechanism and application method thereof
A burr removal and air-gap magnetic technology, applied in abrasive jet machine tools, used abrasive treatment devices, abrasives, etc., can solve problems such as low efficiency, inability to ensure product quality consistency, and inability to completely remove burrs, and achieve savings labor force, guarantee the effect of subsequent use, improve the effect of removal effect
- Summary
- Abstract
- Description
- Claims
- Application Information
AI Technical Summary
Problems solved by technology
Method used
Image
Examples
Embodiment Construction
[0026] The present invention will be further explained below in conjunction with the accompanying drawings and specific embodiments.
[0027] Such as Figure 1 ~ Figure 3 As shown, the present invention provides a deburring mechanism for an air-gap magnetic core, including an air source, a ceramsite release tank 2, a burr removal chamber, a ceramsite recovery tank 6 and a ceramsite recycling device 7, and the ceramsite release tank 2 The release tank cover 21 is provided with a release tank air inlet 22 and a safety valve 23, the gas source is connected to the release tank air inlet 22 through the first conduit 11, and the burr removal chamber includes an upper cavity 3 and a lower cavity 4, and the upper cavity A sealing rubber ring 31 is arranged between the body 3 and the lower cavity body 4, and the two ends of the lower cavity body 4 are respectively provided with a removal chamber air inlet 42 and a removal chamber air outlet 43, and the release tank exhaust port 24 of t...
PUM
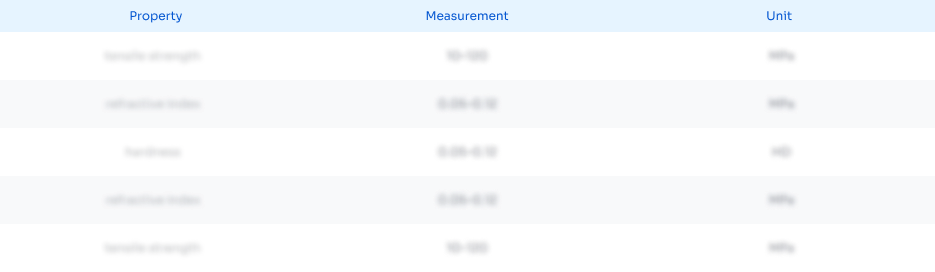
Abstract
Description
Claims
Application Information

- R&D
- Intellectual Property
- Life Sciences
- Materials
- Tech Scout
- Unparalleled Data Quality
- Higher Quality Content
- 60% Fewer Hallucinations
Browse by: Latest US Patents, China's latest patents, Technical Efficacy Thesaurus, Application Domain, Technology Topic, Popular Technical Reports.
© 2025 PatSnap. All rights reserved.Legal|Privacy policy|Modern Slavery Act Transparency Statement|Sitemap|About US| Contact US: help@patsnap.com