Large-area sealing resistance welding process for circumferences of tank body and sealing end cover
A resistance welding, large-area technology, used in resistance welding equipment, welding power sources, welding equipment, etc., can solve the problems of large heat-affected zone, low yield rate, and large equipment footprint, and achieve good pressure resistance and good quality. The effect of high rate and dense weld
- Summary
- Abstract
- Description
- Claims
- Application Information
AI Technical Summary
Problems solved by technology
Method used
Examples
Embodiment 1
[0029] Embodiment 1. When adopting the large-area sealing resistance welding process on the circumference of the tank body and the sealing end cap, the diameter is 63 mm, the angle of the inner chamfer at the end is 10-20 degrees, and the angle of the outer chamfer at the end is 40 degrees. When resistance welding is performed on a tank at -50 degrees, the welding pressure of the capacitor energy storage resistance welding machine is set to 50000N, the first welding voltage of the capacitor energy storage resistance welding machine is set to 530V, and the tempering welding of the capacitor energy storage resistance welding machine The voltage is set to 500V, and the welding peak current of the capacitor energy storage resistance welding machine is set to 350A-400KA; as the preferred chamfer angle, the angle of the inner chamfer at the end of the tank is set to 15 degrees, and the inner chamfer at the end of the tank is The angle is set to 45 degrees.
Embodiment 2
[0030]Embodiment 2: When adopting the large-area sealing resistance welding process of the tank body and the sealing end cover circumference, the diameter is 80 mm, the angle of the inner chamfer of the end is 10-20 degrees, and the angle of the outer chamfer of the end is 40 degrees When resistance welding is performed on a tank at -50 degrees, the welding pressure of the capacitor energy storage resistance welding machine is set to 50000N, the first welding voltage of the capacitor energy storage resistance welding machine is set to 560V, and the tempering welding of the capacitor energy storage resistance welding machine The voltage is set to 540V, and the welding peak current of the capacitor energy storage resistance welding machine is set to 350A-400KA; as the preferred chamfer angle, the inner chamfer at the end of the tank is set to 15 degrees, and the inner chamfer at the end of the tank is set to 45 degree.
[0031] The large-area sealing resistance welding process o...
PUM
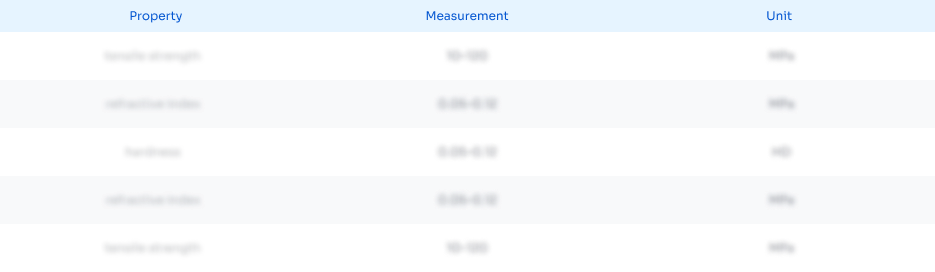
Abstract
Description
Claims
Application Information

- R&D Engineer
- R&D Manager
- IP Professional
- Industry Leading Data Capabilities
- Powerful AI technology
- Patent DNA Extraction
Browse by: Latest US Patents, China's latest patents, Technical Efficacy Thesaurus, Application Domain, Technology Topic, Popular Technical Reports.
© 2024 PatSnap. All rights reserved.Legal|Privacy policy|Modern Slavery Act Transparency Statement|Sitemap|About US| Contact US: help@patsnap.com