Production method for wear-resistant anti-fingerprint film
A production method and anti-fingerprint technology, which is applied in the direction of chemical instruments and methods, layered products, synthetic resin layered products, etc., can solve the problems of unstable product quality, easy to appear bubbles, and film connection falling off, etc., to achieve the function of improvement Sex and practicability, strong hydrophobic effect
- Summary
- Abstract
- Description
- Claims
- Application Information
AI Technical Summary
Problems solved by technology
Method used
Image
Examples
Embodiment 1
[0025] A production method for a friction-resistant and anti-fingerprint film, comprising the following steps:
[0026] Step 1: Select a large-area substrate, the substrate is made of glass or resin plastic, and the selected substrate needs to be illuminated and laser-detected without damage cracks;
[0027] Step 2: Cut the substrate, grind and polish the cutting edge of the substrate to make the corners smooth and arc-shaped, and repeatedly clean both sides of the substrate. The cleaning solution is mixed with 1L of distilled water and 8ml of detergent. After cleaning, both sides of the substrate have no burrs, no dust and no sand particles, and the smoothness and cleanliness are good;
[0028] Step 3: Dry the substrate. Place the substrate in the dryer for drying. There is no obvious air flow at the drying position of the substrate. The drying temperature of the substrate is maintained between 40°C to maintain the drying efficiency of the substrate and avoid The drying heat...
Embodiment 2
[0033] A production method for a friction-resistant and anti-fingerprint film, comprising the following steps:
[0034] Step 1: Select a large-area substrate, the substrate is made of glass or resin plastic, and the selected substrate needs to be illuminated and laser-detected without damage cracks;
[0035] Step 2: Cut the substrate, grind and polish the cutting edge of the substrate to make the corners smooth and arc-shaped, and repeatedly clean the two sides of the substrate. The cleaning solution is mixed with 1L of distilled water and 10ml of detergent. After cleaning, both sides of the substrate have no burrs, no dust and no sand particles, and the smoothness and cleanliness are good;
[0036] Step 3: Dry the substrate. Place the substrate in the dryer for drying. There is no obvious air flow at the drying position of the substrate. The drying temperature of the substrate is maintained between 50°C to maintain the drying efficiency of the substrate and avoid The drying ...
Embodiment 3
[0041] A production method for a friction-resistant and anti-fingerprint film, comprising the following steps:
[0042] Step 1: Select a large-area substrate, the substrate is made of glass or resin plastic, and the selected substrate needs to be illuminated and laser-detected without damage cracks;
[0043] Step 2: Cut the substrate, grind and polish the cutting edge of the substrate to make the corners smooth and arc-shaped, and repeatedly clean both sides of the substrate. The cleaning solution is mixed with 1L of distilled water and 8ml of detergent. After cleaning, both sides of the substrate have no burrs, no dust and no sand particles, and the smoothness and cleanliness are good;
[0044] Step 3: Dry the substrate. Place the substrate in the dryer for drying. There is no obvious air flow at the drying position of the substrate. The drying temperature of the substrate is maintained between 50°C to maintain the drying efficiency of the substrate and avoid The drying heat...
PUM
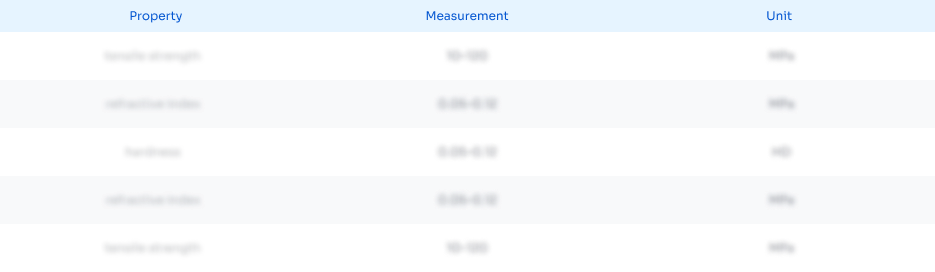
Abstract
Description
Claims
Application Information

- R&D Engineer
- R&D Manager
- IP Professional
- Industry Leading Data Capabilities
- Powerful AI technology
- Patent DNA Extraction
Browse by: Latest US Patents, China's latest patents, Technical Efficacy Thesaurus, Application Domain, Technology Topic, Popular Technical Reports.
© 2024 PatSnap. All rights reserved.Legal|Privacy policy|Modern Slavery Act Transparency Statement|Sitemap|About US| Contact US: help@patsnap.com