A method for preparing low-carbon olefins by catalytic synthesis gas conversion
A technology for syngas conversion and low-carbon olefins, which is applied in the field of catalysis and can solve problems such as cumbersome steps, harsh reaction conditions, and mismatched reaction temperatures
- Summary
- Abstract
- Description
- Claims
- Application Information
AI Technical Summary
Problems solved by technology
Method used
Examples
Embodiment 1
[0017] 1. According to Fe / Zn molar ratio is 1:1, Na / (Fe+Zn) mass ratio is 3%, 100mL 1mol / L FeSO 4 ·7H 2 O aqueous solution and 100mL 1mol / L Zn(NO 3 ) 3 ·6H 2 O aqueous solution was mixed and stirred for half an hour, and then 2mol / L Na was added dropwise 2 CO 3 The aqueous solution is used as a precipitating agent, the pH of the system is controlled to be 9, and co-precipitation is carried out at 80°C. After the precipitation is completed, it is aged at a constant temperature for 4 hours. After the aging, the precipitate is filtered and washed, dried in an oven at 60° C., and then calcined at 400° C. for 4 hours to prepare a FeZnNa catalyst.
[0018] 2. Put 1.85g of β molecular sieve in 50mL of 0.25mol / L NaOH aqueous solution, put it into a hydrothermal kettle lined with polytetrafluoroethylene, transfer it into an oven, and conduct hydrothermal treatment at 150°C for 21h. After the reaction was completed, the catalyst was taken out, washed, filtered and dried, and calci...
Embodiment 2
[0021] In this example, according to the molar ratio of Fe / Zn being 2:1 and the mass ratio of Na / (Fe+Zn) being 3%, the FeZnNa catalyst was prepared by the method in step 1 of Example 1. And after preparing the Naβ molecular sieve catalyst according to the method of step 2 of Example 1, the reaction of catalyzing synthesis gas to prepare light olefins was carried out according to the method of step 3 of Example 1, and the results are shown in Table 1.
Embodiment 3
[0023] In this example, the FeZnNa catalyst was prepared according to the method in Step 1 of Example 1. When preparing the Naβ molecular sieve catalyst, the concentration of the NaOH aqueous solution used was 0.5 mol / L, and other steps were the same as step 2 of Example 1. Then, according to the method in step 3 of Example 1, the reaction of preparing light olefins from catalytic synthesis gas was carried out, and the results are shown in Table 1.
PUM
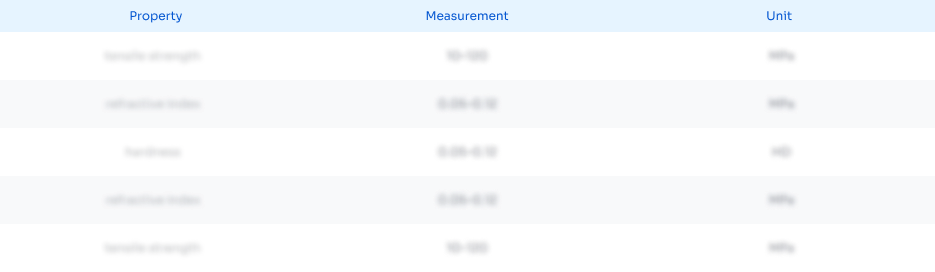
Abstract
Description
Claims
Application Information

- R&D Engineer
- R&D Manager
- IP Professional
- Industry Leading Data Capabilities
- Powerful AI technology
- Patent DNA Extraction
Browse by: Latest US Patents, China's latest patents, Technical Efficacy Thesaurus, Application Domain, Technology Topic, Popular Technical Reports.
© 2024 PatSnap. All rights reserved.Legal|Privacy policy|Modern Slavery Act Transparency Statement|Sitemap|About US| Contact US: help@patsnap.com