Method for preparing hydrofining catalyst
A hydrofining and catalyst technology, applied in chemical instruments and methods, catalyst activation/preparation, heterogeneous catalyst chemical elements, etc. Issues such as high phase active metal content
- Summary
- Abstract
- Description
- Claims
- Application Information
AI Technical Summary
Problems solved by technology
Method used
Examples
Embodiment 1
[0048] Nickel chloride, ammonium metatungstate are added respectively to dissolving tank 1 that deionized water is housed, and mixed solution A is mixed, and the weight concentration of Ni in NiO in mixed solution A is 28g / L, and W is expressed as WO 3 The weight concentration of meter is 27g / L. Ammonium metatungstate, ammonium molybdate, and aluminum chloride were respectively added to the dissolving tank 2 equipped with deionized water to prepare a mixed solution B. In the mixed solution B, W was replaced by WO 3 The weight concentration of Mo is 30g / L, Mo is MoO 3 The weight concentration is 36g / L, Al is expressed as Al 2 o 3 The weight concentration of meter is 26g / L. Deionized water is added in the reaction tank, and the weight concentration is based on Al 2 o 3 Add 30g / L sodium metaaluminate solution and mixed solution A into the reaction tank in parallel flow, keep the gelling temperature at 62°C, control the pH value at 7.8 during the co-flow gelling reaction proc...
Embodiment 2
[0050] According to the method of embodiment 1, press the component content ratio of catalyst B in table 1, add nickel chloride, ammonium metatungstate, zirconium oxychloride solution in dissolution tank 1, prepare mixed solution A, add to dissolution tank 2. Add ammonium metatungstate, ammonium molybdate and aluminum nitrate to prepare mixed solution B. Deionized water is added in the reaction tank, and the weight concentration is based on Al 2 o 3 40g / L sodium metaaluminate solution and mixed solution A are added into the reaction tank in parallel flow, the gelling temperature is kept at 45°C, the pH value is controlled at 7.6 during the concurrent gelling reaction process, and the gelling time is controlled at 1.2 hours , Generate slurry I containing nickel, tungsten, aluminum, zirconium precipitate. The obtained precipitate slurry I was aged under stirring, the stirring speed was 170 rpm, the aging temperature was 74° C., the aging pH value was controlled at 7.2, and the...
Embodiment 3
[0052] According to the method of Example 1, according to the composition ratio of the catalyst C in Table 1, nickel nitrate and ammonium metatungstate solution are added to the dissolution tank 1 to prepare a mixed solution A, and metatungstate is added to the dissolution tank 2 Ammonium, ammonium molybdate, and aluminum chloride are used to prepare mixed solution B. Deionized water is added in the reaction tank, and the weight concentration is based on Al 2 o 3 36g / L sodium metaaluminate solution and mixed solution A are added into the reaction tank in parallel flow, the gelling temperature is kept at 50°C, the pH value is controlled at 7.9 during the co-current gelling reaction process, and the gelling time is controlled at 1.0 hour , Generate slurry I containing nickel, tungsten, and aluminum precipitates. The obtained precipitate slurry I was aged under stirring, the stirring speed was 220 rpm, the aging temperature was 72° C., the aging pH value was controlled at 6.9, ...
PUM
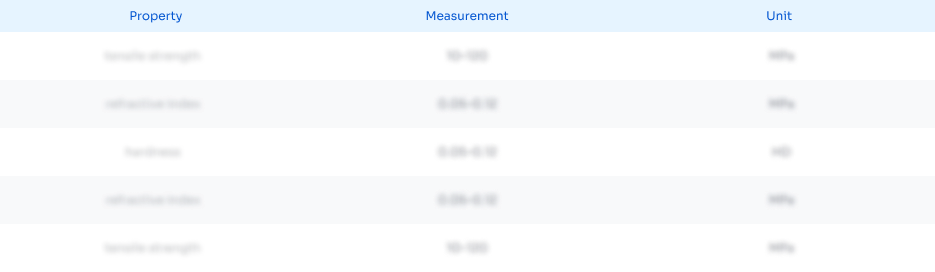
Abstract
Description
Claims
Application Information

- R&D
- Intellectual Property
- Life Sciences
- Materials
- Tech Scout
- Unparalleled Data Quality
- Higher Quality Content
- 60% Fewer Hallucinations
Browse by: Latest US Patents, China's latest patents, Technical Efficacy Thesaurus, Application Domain, Technology Topic, Popular Technical Reports.
© 2025 PatSnap. All rights reserved.Legal|Privacy policy|Modern Slavery Act Transparency Statement|Sitemap|About US| Contact US: help@patsnap.com