Multi-material synchronous fed FDM spray head
A multi-material, feeding technology, used in additive processing, coating devices, 3D object support structures, etc., can solve the problems of limited heating temperature, inability to achieve printing, difficult to guarantee accuracy, etc., to save the positioning required. time, shorten the dwell time, avoid the effect of position error
- Summary
- Abstract
- Description
- Claims
- Application Information
AI Technical Summary
Problems solved by technology
Method used
Image
Examples
Embodiment Construction
[0023] In order to make the object, technical solution and advantages of the present invention clearer, the present invention will be further described in detail below in conjunction with the accompanying drawings and embodiments. It should be understood that the specific embodiments described here are only used to explain the present invention, not to limit the present invention. In addition, the technical features involved in the various embodiments of the present invention described below can be combined with each other as long as they do not constitute a conflict with each other.
[0024] figure 1 It is a schematic diagram of the overall structure of the melt extrusion nozzle constructed according to the embodiment of the present invention, such as figure 1 As shown, the present invention provides a multi-material fused deposition feed and melt extrusion nozzle, the device includes a feed unit 1 , an agitator 2 , an air pressure extrusion unit 3 , a heater 4 , a nozzle 5 ...
PUM
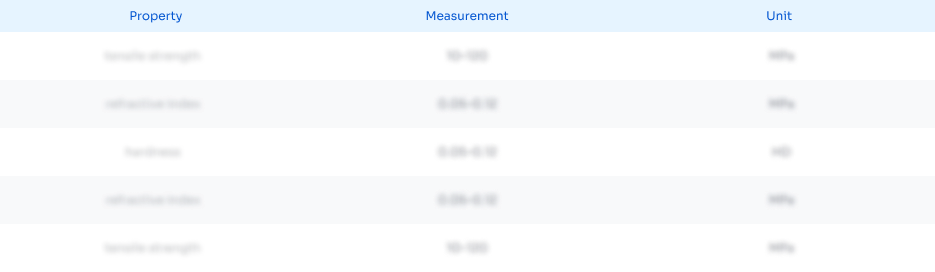
Abstract
Description
Claims
Application Information

- Generate Ideas
- Intellectual Property
- Life Sciences
- Materials
- Tech Scout
- Unparalleled Data Quality
- Higher Quality Content
- 60% Fewer Hallucinations
Browse by: Latest US Patents, China's latest patents, Technical Efficacy Thesaurus, Application Domain, Technology Topic, Popular Technical Reports.
© 2025 PatSnap. All rights reserved.Legal|Privacy policy|Modern Slavery Act Transparency Statement|Sitemap|About US| Contact US: help@patsnap.com