High-temperature smoke third-incineration and waste heat utilization all-in-one device for SRL furnace
A high-temperature flue gas and waste heat technology, applied in the direction of non-flammable liquid/gas transportation, incinerators, combustion chambers, etc., can solve the problem of unfavorable dioxin re-synthesis control, high installation cost and complexity, and low utilization rate of combustion-supporting air Advanced problems, to achieve the effect of reducing the air excess coefficient and flue gas volume, improving the efficiency of waste heat recovery, and high heat recovery utilization rate
- Summary
- Abstract
- Description
- Claims
- Application Information
AI Technical Summary
Problems solved by technology
Method used
Image
Examples
Embodiment Construction
[0030] The present invention will be described in detail below in conjunction with the accompanying drawings.
[0031] Such as Figure 1-3 As shown, the present invention discloses an integrated device for tertiary incineration and waste heat utilization of high-temperature flue gas of SRL furnace. The heat of the flue gas produces a certain grade of steam, and cools and separates a large amount of dust contained in the flue gas. It includes a stable cavity supported by a stand 13. The cavity is spliced by membrane water cooling walls. The membrane water cooling wall is divided into an upper arch membrane water cooling wall 7 and a side membrane water cooling wall 12. The upper arch membrane The water-cooled wall includes an integrally formed vault and side walls arranged on both sides of the vault, and the side membrane water-cooled wall is assembled and closed at both ends of the upper arched membrane water-cooled wall to form a cavity. A drum 5 is supported above the ca...
PUM
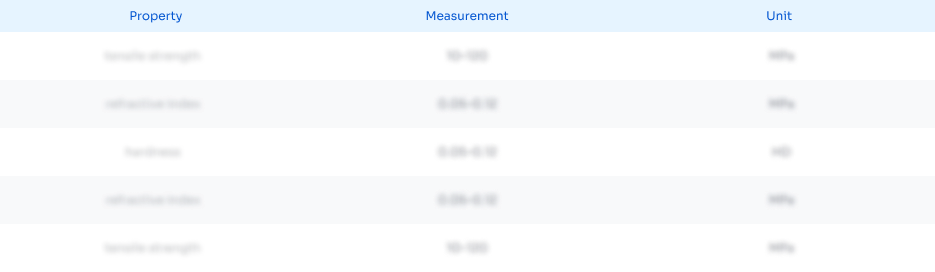
Abstract
Description
Claims
Application Information

- R&D Engineer
- R&D Manager
- IP Professional
- Industry Leading Data Capabilities
- Powerful AI technology
- Patent DNA Extraction
Browse by: Latest US Patents, China's latest patents, Technical Efficacy Thesaurus, Application Domain, Technology Topic, Popular Technical Reports.
© 2024 PatSnap. All rights reserved.Legal|Privacy policy|Modern Slavery Act Transparency Statement|Sitemap|About US| Contact US: help@patsnap.com