3D printing path planning method of continuous fiber reinforced composite material
A technology for enhancing composite materials and 3D printing. It is used in additive processing, manufacturing auxiliary devices, and processing data acquisition/processing. It can solve problems such as poor printing accuracy, mechanical properties of composite materials that do not consider the fiber printing direction, and low printing quality. , to achieve the effect of improving the mechanical properties
- Summary
- Abstract
- Description
- Claims
- Application Information
AI Technical Summary
Problems solved by technology
Method used
Image
Examples
Embodiment Construction
[0031] The following will clearly and completely describe the technical solutions in the embodiments of the present invention with reference to the accompanying drawings in the embodiments of the present invention. Obviously, the described embodiments are only some of the embodiments of the present invention, not all of them. The following description of at least one exemplary embodiment is merely illustrative in nature and in no way taken as limiting the invention, its application or uses. Based on the embodiments of the present invention, all other embodiments obtained by persons of ordinary skill in the art without creative efforts fall within the protection scope of the present invention.
[0032] Such as figure 1 As shown, the present invention proposes a continuous fiber reinforced composite material 3D printing path planning method, which establishes a three-dimensional model according to the actual size of the target component, and obtains the layer and contour informa...
PUM
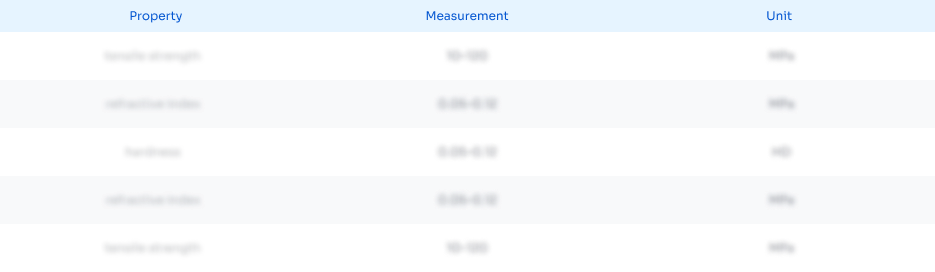
Abstract
Description
Claims
Application Information

- Generate Ideas
- Intellectual Property
- Life Sciences
- Materials
- Tech Scout
- Unparalleled Data Quality
- Higher Quality Content
- 60% Fewer Hallucinations
Browse by: Latest US Patents, China's latest patents, Technical Efficacy Thesaurus, Application Domain, Technology Topic, Popular Technical Reports.
© 2025 PatSnap. All rights reserved.Legal|Privacy policy|Modern Slavery Act Transparency Statement|Sitemap|About US| Contact US: help@patsnap.com